
Warehouse Layout Design 101: Optimizing Efficiency, Safety, and Comfort

Designing a warehouse that runs smoothly takes careful planning. A smart layout helps keep operations efficient, storage organized, and the workspace safe. Every design choice affects how well things flow, how much energy the building uses, and the overall cost of running it. When done right, the layout can boost productivity, support green building goals, and create a better work environment.
Designing a Functional and Adaptable Warehouse Layout
A good warehouse layout should be both efficient and flexible, making it easy for materials, products, and people to move around. The receiving area should allow for quick unloading and inspection, with direct paths to storage zones set up for the specific types of inventory. Poor layouts can slow things down, cause backups, and make it harder to find and move items when needed.
Improving How Work Gets Done in the Warehouse
To avoid delays and confusion, many warehouses use layouts like U-shapes, I-shapes, or L-shapes. These setups help direct the flow of goods and reduce traffic jams. Adding automation—like conveyor belts or robots—can take things a step further. But planning for automation means thinking ahead. Warehouses with modular storage and flexible shelving can more easily adapt to new technologies like robotics and smart inventory systems.
Optimizing Storage and Safety in Warehouse Design
Smart storage solutions are key to using space wisely. Choosing the right shelving, racking, and storage setups helps maximize space without making things hard to reach. What you’re storing makes a difference—bulkier items might need drive-in racking, while smaller, fast-moving products work better with bin shelving or vertical lift systems.
Integrating Safety into Warehouse Design from the Start
Safety should be built into the design from the beginning. Marked walkways, slip-resistant floors, and automatic hazard detectors help prevent accidents. Fire safety systems also need to be part of the plan, especially in areas storing flammable materials. Meeting OSHA guidelines with proper exits, good airflow, and ergonomic workstations not only keeps things compliant but also makes daily work easier and safer.
Zoning and Hazard Management for Safer Operations
A smart layout also separates high-risk areas. Cold storage zones should have insulation and ventilation to stop moisture buildup. Hazardous material zones need special features like spill containment systems. These details improve safety and also help prevent major disruptions if something goes wrong.
Enhancing Energy Efficiency and Comfort in Warehouse Layouts
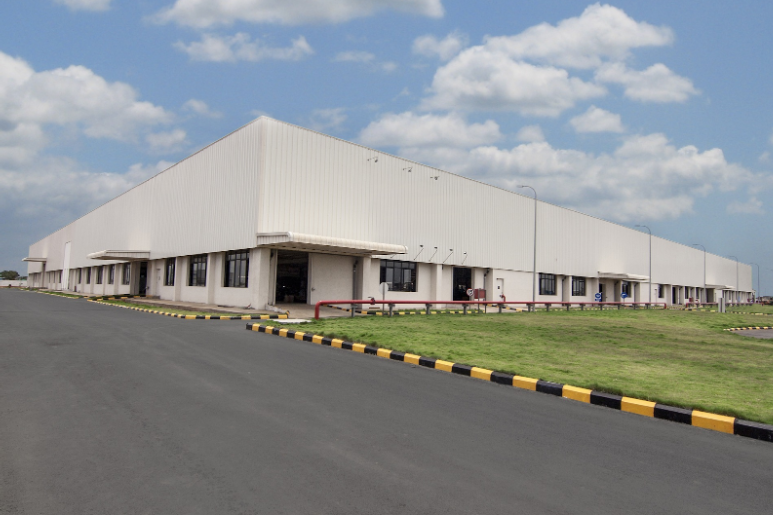
Today’s warehouses aim to do more than store goods—they also aim to save energy. Good insulation, efficient lighting, and smart climate controls can cut down on energy use and reduce the building’s environmental impact. Using insulated concrete forms (ICFs) enhances superior thermal efficiency, helping to keep temperatures steady and reducing the need for excessive heating and cooling.
Keeping a stable indoor temperature is especially important for things like medicine or perishable foods. ICFs provide superior thermal efficiency that helps maintain those critical conditions with less energy use. Plus, a comfortable temperature helps workers stay focused and avoid fatigue from temperature swings.
Lowering Energy Evaluations for Sustainable Warehouse Construction
Getting a lower energy evaluation rating is a top goal for eco-conscious businesses. Features like airtight construction, natural lighting, and efficient HVAC systems all help. Adding solar panels, geothermal heating, and top-tier insulation like ICFs can bring energy use close to zero.
Some warehouses are even using flooring that captures energy from footsteps and forklifts to power lights or security systems. These innovations show that sustainable design doesn’t just save energy—it can actively support daily operations.
Boosting Security and Structural Integrity in Warehouse Design
Security is just as important as layout. Tools like access controls, surveillance systems, and strong perimeters keep people and products safe. But materials matter too. What the building is made of can protect against weather and outside threats.
Using ICFs for Security and Longevity
ICFs are tough and long-lasting, making warehouses better equipped to handle severe weather or impacts. Unlike steel frames, which can rust, ICF structures hold up better during hurricanes, earthquakes, and even fires. That strength means fewer repairs and lower maintenance costs over time.
For warehouses in high-risk zones, ICFs offer a real advantage. Their strength against shaking and shifting makes them a smart choice in earthquake-prone areas. Plus, ICF walls can withstand fire for over four hours—critical for industries with high fire risks.
Strategies for Designing a Future-Proof Warehouse Layout
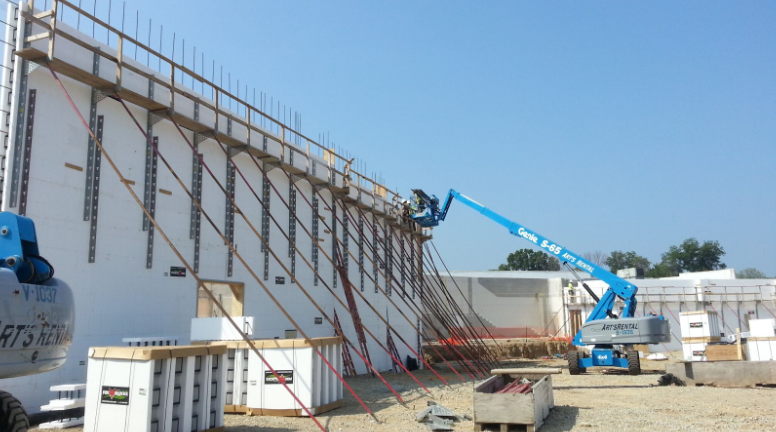
A future-ready warehouse should be easy to update as business needs change. Facilities dealing with seasonal changes, new product types, or tech upgrades should have flexible features. Modular storage, adjustable racks, and dynamic shelving make it easier to grow without tearing things down.
As more automation enters the picture, building in space for robots, smart inventory tools, and data analytics helps a warehouse stay up to date. Some warehouses are going fully automated—so-called “dark warehouses” that don’t need people on-site. While that’s not for everyone, planning for at least some automation can keep your operation competitive. ICF wall assemblies may be designed for tall walls and for the support of long span roof structures, enabling any warehouse configuration.
Build a Smarter Warehouse with Fox Blocks
An optimized warehouse layout is more than a blueprint—it’s an investment in efficiency, sustainability, and security. Fox Blocks’ insulated concrete forms offer a superior solution for energy-efficient, durable, and adaptable warehouse construction. Contact us today for more information.