
How to Build a Warehouse the Right Way

In today's fast-paced market, having an efficient warehouse is key for businesses to stay ahead. When planning to build a warehouse, a well-thought-out strategy helps to ensure that the finished warehouse will be highly functional, durable, and cost-effective. Knowing the core steps to building a warehouse, key factors to consider, and the critical role of material selection will prepare you for a successful warehouse building project.
Planning Your Warehouse: Laying a Strong Foundation
Any successful warehouse build starts with good planning. Spending extra time and effort on this stage will reap benefits during the actual construction of the warehouse.
Location Selection
The phrase "Location, location, location" rings true when planning where to build a warehouse. The site should have easy access to major transportation routes, and it’s important to consider proximity to suppliers, customers, and the workforce. Analyzing the local labor market and regulatory landscape is also vital to avoid any unforeseen challenges.
Design and Layout
A well-designed layout is the backbone of an efficient warehouse. It's essential to consider the flow of goods, from receiving to shipping, and ensure that there is ample space for storage, sorting, and handling. Another key design element is climate control for not only staff but the products and the operational costs. Engaging with professionals who have experience in warehouse design can provide invaluable insights.
Size and Scalability
The size of the warehouse should not only meet your current needs, but also accommodate future growth. Building a warehouse is a large capital expenditure and it should be strategic. Warehouses can often be built with the future in mind while limiting the build-out to what is needed presently. Scalability is crucial to adapt to changing business dynamics.
Crafting the Timeline: How Long to Build a Warehouse
The timeline to build a warehouse can vary significantly based on the size, design, and location. It's vital to have a clear schedule from the outset, that considers the time for permits, construction, and any potential contingencies. Material selection and availability, as well as contractor timelines, will greatly impact the desired timeline.
Engaging with a professional construction team with experience in warehouse building can help streamline the process and avoid costly delays. Getting the initial timeline prepared is often an iterative process, so expect to have to revise the timeline as new information is learned.
Material Selection: Weighing Cost and Performance
When it comes to material selection, availability of materials, qualified labor, and cost, are all considerations that come into play. Material selection also has a big impact on the timeline. Common materials used to build warehouses include:
- Metal Frame
- Wood Studs
- Concrete Block (CMU)
- Insulated Concrete Forms (ICF)
Metal Frame
Due to their durability and relatively low cost, metal warehouses have exploded in popularity. Metal warehouses can be quickly constructed but require crews experienced in building metal frame buildings. Metal warehouses are durable, but can be susceptible to moisture damage and have little natural insulation properties.
CMU
Masonry walls are a common application for warehouse construction. Skilled labor is required to install these walls. CMU walls may be unfinished with no insulation providing no thermal efficiency.
Wood Studs
Wood is a convenient choice due to the availability of skilled carpenter crews knowledgeable in building with wood. The price of wood has skyrocketed in recent years which can balloon total warehouse building costs. Warehouse designs typically have tall walls, wood framing may not be compatible for tall wall structures. Wood is also not as durable as a metal warehouse and is susceptible to pests and moisture damage. These factors have led to wood stud warehouses falling in popularity.
Insulated Concrete Forms
Insulated concrete forms provide a good blend of strength, durability, and low cost to warehouse builds. ICF blocks consist of two foam sheets of insulation held together with a system of ties to form a hollow space between the sheets. The lightweight blocks are stacked on site and rebar is placed in the hollow cavity formed between the sheets. Concrete is then poured into the hollow space and allowed to set. The resulting steel-reinforced concrete structure is incredibly structurally sound, resilient, durable, and high-performing.
The Advantage of Insulated Concrete Forms (ICFs)
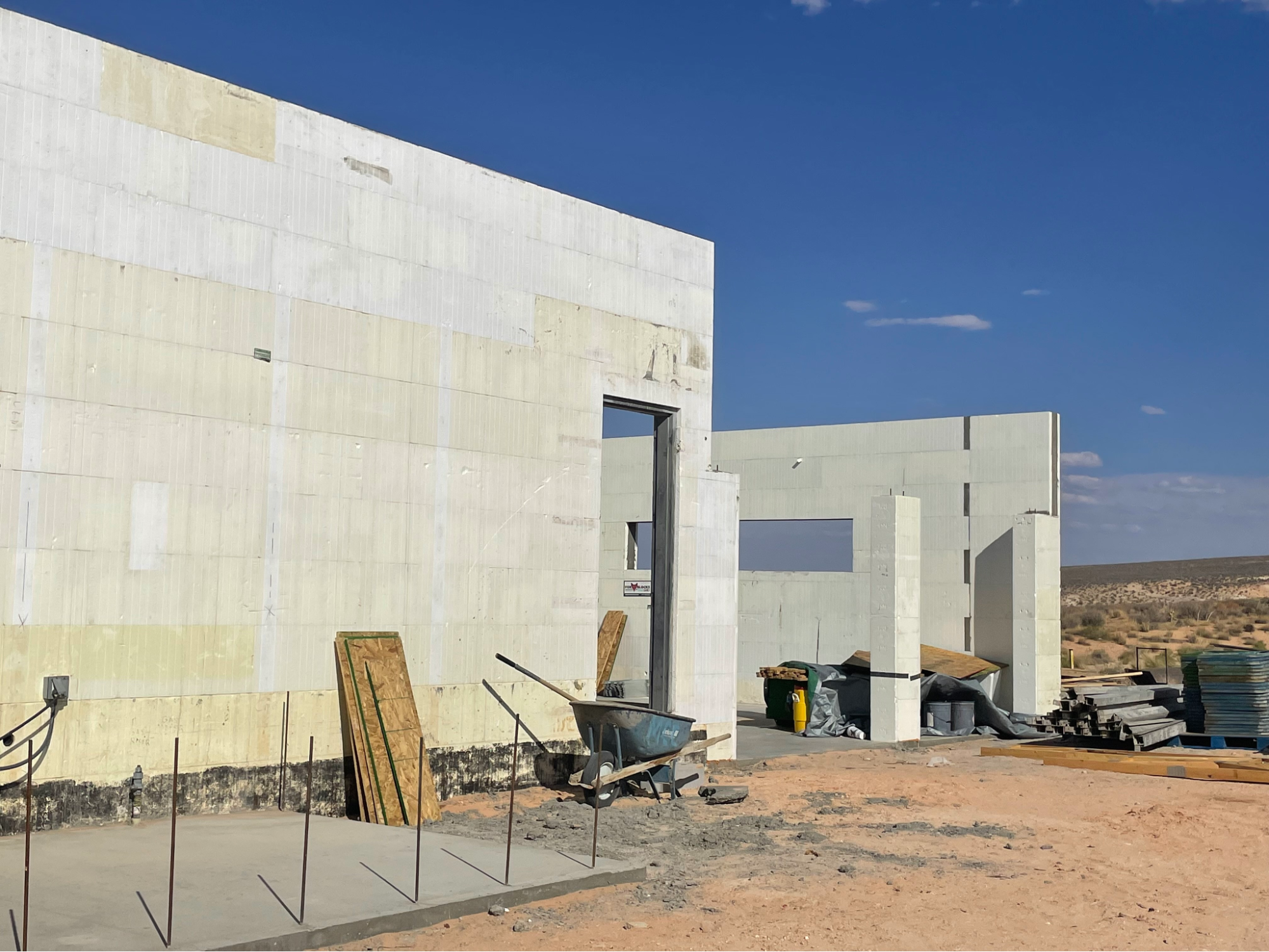
ICF blocks are emerging as a superior choice for building durable and energy-efficient warehouses. After installation, the large mass of steel-reinforced concrete with both interior and exterior layers of continuous insulation results in big benefits for the warehouse.
Energy Efficiency
One of the stellar advantages of ICFs is their exceptional energy efficiency. The insulation properties significantly reduce heating and cooling costs, which makes a substantial difference in operational expenses over time. The thermal mass of ICFs stabilizes the interior temperature, which creates a comfortable working environment plus the ability to provide climate control for products year-round.
Durability
ICFs are known for their remarkable durability, ability to withstand extreme weather conditions, and potential impacts within a bustling warehouse environment. This durability translates to lower maintenance costs, inventory and personal protection and a longer lifespan for your warehouse.
Ease of Construction
ICF blocks are naturally easy to build with, and require less specialized crews. The ICF construction method naturally limits human error and is easier on crews: the blocks are lightweight and easy to move around a job site. Concrete is also often locally sourced and readily available. ICF wall assemblies have been seen used for tall walls, as high as 30 to 40 feet and in multi-story buildings. The reinforced concrete walls accept point loads from beams and, in most cases, without pilasters. A Fox Blocks wall assembly will accept any code approved interior of exterior finishing material.
Choose Fox Blocks for a Better Warehouse
When building a warehouse, choosing the right materials and partners is crucial. Fox Blocks offers a range of ICF products that are ideal for constructing a resilient and energy-efficient warehouse.
With a focus on sustainable and cost-effective construction solutions, Fox Blocks is your go-to partner for your warehouse construction needs. Explore their range of ICF products and discover how they can elevate your warehouse project to the next level.
Reach out to their ICF experts today to learn why Fox Blocks gives you an advantage in your next warehouse build!