
Constructing an ICF Garage Foundation

A garage is only as strong as the foundation beneath it. Without the right planning and construction, problems like settling, water damage, and instability can show up over time. Knowing how to build a garage foundation with Insulated Concrete Forms (ICFs) can help you create a solid, energy-efficient space that’s built to last and meets today’s building standards.
Site Evaluation and Preparation
Good site prep is key to a stable, long-lasting garage foundation. Before any concrete work starts, the ground needs to be checked, cleared, and reinforced to help avoid settling and future structural problems.
Soil Evaluation and Excavation
It all starts with checking the soil. Builders need to know how well the soil can support weight. If it’s loose or expands easily, it can cause the foundation to shift over time, so compacting the ground is critical. Many builders use gravel or crushed stone to improve drainage and give the foundation a stable base. After that, excavation clears the area and digs to the right depth, based on how deep the frost line goes in your region. Proper grading also helps steer rainwater away from the foundation instead of letting it pool around the edges.
Laying the Footings and Preparing for ICF Walls
Once the site is ready, the footings go in. These support the entire structure, so they need to match the garage’s weight and design. Reinforcing them with steel rebar helps prevent cracking and adds strength. Depending on local soil conditions or building rules, some garages may need deeper footings or extra reinforcement. After the footings are poured and cured, you can start putting together the foundation walls using ICF blocks—an upgrade from concrete formwork or masonry block.
The Benefits of ICF for Garage Foundations
If you want a stronger, more efficient foundation, ICFs are worth a close look. These interlocking blocks form a tight insulation layer that keeps heat in and cold out. The concrete inside also helps regulate temperature swings, cutting down on the energy needed to heat and cool the garage.
ICFs stand up better to moisture than traditional materials, which helps prevent issues like mold, rot, or water seepage. That makes for a solid, dry foundation that lasts. Plus, the higher R-value of ICFs gives better insulation than regular poured concrete, helping lower energy bills and making the garage more comfortable to use.
That comfort is a big bonus—especially if your garage doubles as a workshop, gym, or living space. ICFs help maintain steady indoor temps, getting rid of drafts and cold spots. Better thermal performance means lower utility costs and a more comfortable space all year long.
Building the ICF Garage Foundation
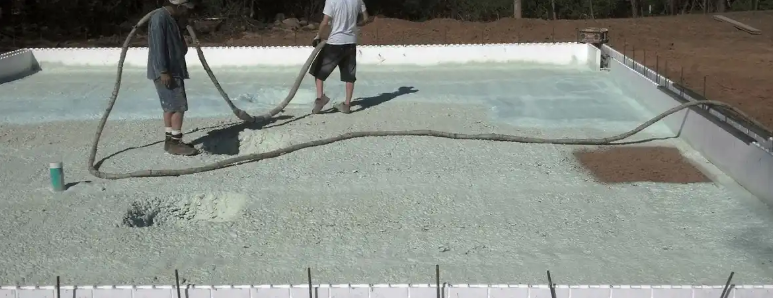
To build a garage foundation with ICFs, you need to be precise, follow reinforcement guidelines, and carry out each step carefully to ensure long-term strength. From stacking the forms to pouring and curing the concrete, each part of the process plays a major role in how well the foundation holds up.
Stacking and Reinforcing the ICF Walls
Assembling the ICF Blocks
Once the footings are cured, the ICF blocks with a 6" or 8" concrete core are stacked to form the walls. They have to be aligned correctly and locked tightly together. You also need to plan ahead for utility openings like plumbing or electrical, and make sure they’re worked into the forms.
Securing the Structure with Rebar Reinforcement
Next comes the steel reinforcement—rebar is added both vertically and horizontally. How thick and how far apart the rebar is depends on how much weight the garage will carry and any earthquake safety requirements. Typically the reinforcement would be #4 or #5 rebar depending on the loads. When you combine steel and concrete inside ICFs, the result is a very strong foundation that can handle heavy loads.
Pouring and Curing the Concrete
Executing a Proper Concrete Pour
With the ICFs in place, concrete is poured in layers to avoid putting too much pressure on the forms. It’s important to choose the right mix—ICF-friendly concrete typically has a slump rating of 5 to 6 inches so it flows properly. Using a mechanical vibrator helps remove air pockets so the concrete sets evenly.
Curing for Maximum Strength
Curing is key to making the concrete strong. It needs to stay moist and protected from extreme temperatures. The ICFs naturally create a controlled environment for curing, which helps prevent cracking and ensures the concrete hardens the right way. Once cured, the walls are waterproofed to keep moisture out and help the foundation last.
Drainage and Waterproofing Considerations
Good drainage and waterproofing are essential to keep water away from the foundation and prevent long-term problems like cracks, mold, or shifting.
Installing a Perimeter Drainage System
After curing, a quality drainage system is installed to manage how water flows around the structure. A perimeter drain tile is usually placed around the base to carry water away. Builders also backfill with at least 6 inches of washed gravel to help moisture drain out instead of collecting near the foundation.
Applying Waterproofing Barriers
To protect against moisture even more, builders often apply waterproof coatings or membranes to the walls. Under the garage slab, a vapor barrier adds another layer of protection, reducing the risk of condensation. These steps prevent pressure from building up beneath the foundation, which helps avoid leaks or shifting later on.
Finalizing the Foundation and Backfilling
Once everything is cured and waterproofed, backfilling finishes the job. Done right, it protects the foundation from erosion, shifting, and water intrusion, setting it up for long-term success.
Compacting the Soil for Stability
The soil around the foundation should be added in layers and compacted as you go. If you just dump in loose dirt, it can shift later and lead to cracks or movement in the foundation. Careful compaction ensures steady support.
Site Grading for Water Management
After backfilling, the site should be graded to slope away from the garage. This helps water drain off naturally, instead of collecting around the foundation. Proper grading is a big part of protecting against frost heave, erosion, and long-term moisture problems.
If you want a foundation that’s energy-efficient, comfortable, and built to last, learning how to build with ICFs is a smart investment. With better insulation, added durability, and moisture resistance, ICFs offer more benefits than traditional foundation methods.
Achieving Energy Efficiency and Structural Security
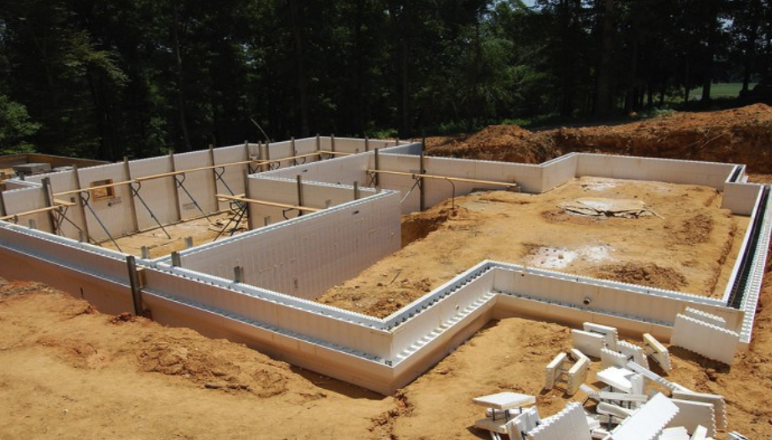
A well-built garage foundation does more than hold up your structure—it can also improve energy efficiency and stand up to wear over time.
Maximizing Energy Efficiency with ICF Foundations
If you’re aiming to meet today’s energy codes, ICFs help get you there. These foundations contribute to lower HERS (Home Energy Rating System) scores, which are a key part of energy-efficient construction. They also reduce thermal bridging, which keeps heat from escaping and makes indoor temps more stable.
Superior Strength and Disaster Resilience
ICFs don’t just save energy—they’re also incredibly strong. Unlike traditional materials that can wear down, ICFs resist fire, pests, and severe weather. They also hold up better to impacts, making them a smart choice for areas prone to hurricanes or earthquakes. A garage foundation built with ICF technology offers better protection from disasters and long-term exposure to the elements.
Choose Fox Blocks for a Stronger, Longer-Lasting Garage Foundation
A properly constructed foundation is essential for a garage that stands the test of time. Fox Blocks provides high-performance ICF solutions that deliver unmatched strength, durability, and energy efficiency for any garage project. If you're ready to take the next step in how to build a garage foundation that lasts, contact us today for more information.