
Understanding Current Supply Chain Woes and the Lack of Skilled and Unskilled Labor

In 2022, builders, construction companies, and developers can look forward to an estimated compound annual growth rate (CAGR) for new construction, additions, alterations, maintenance, and repairs of 12.7 percent. In addition, the recently approved $1.2 trillion infrastructure bill offers significant opportunities for construction companies to hire employees and grow their businesses.
What’s in the Infrastructure Bill?
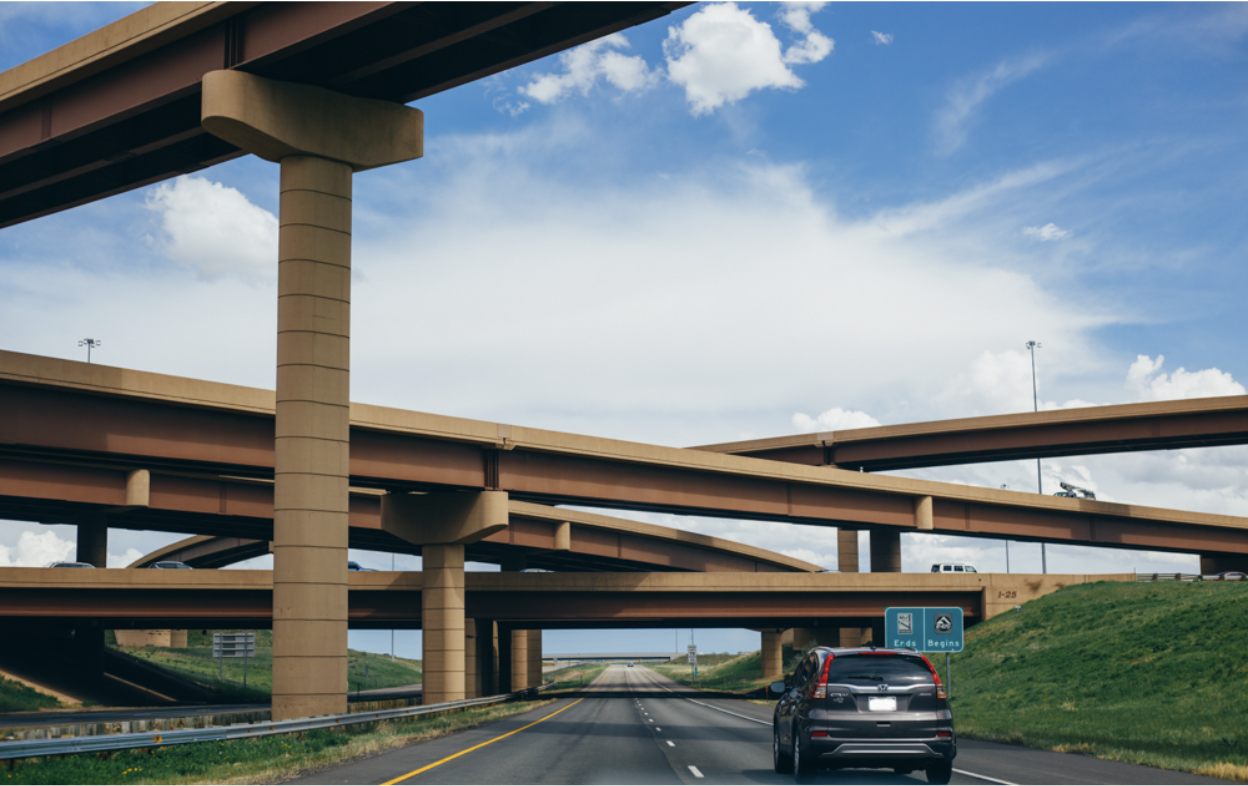
The infrastructure bill aims to improve travel safety, ensure efficient transportation of goods and produce, and upgrade utility systems (electric, internet, water). Highlights of the bill include:
$110 billion for roads, bridges, and major infrastructure projects
$39 billion to upgrade and expand public transit
$66 billion in passenger and freight rail
$17 billion for port infrastructure and $25 billion in airports
$65 billion to enhance the nation’s broadband infrastructure
$65 billion to rebuild the electric grid and expand renewable energy
$55 billion to upgrade the water infrastructure, replace lead service lines and pipes
$50 billion to improve the system’s resilience to drought, floods, and cyberattacks
Labor Shortages and Supply Chain Problems Slow Construction
Unfortunately, builders and construction companies will struggle to take advantage of these unprecedented construction opportunities due to labor shortages and supply chain problems. Both challenge companies to schedule projects, driving some even to turn down work.
To benefit from the current construction market, contractors and building companies must redirect their construction practices towards cost-effective building materials and less labor-intensive construction methods, like Fox Blocks insulated concrete forms (ICFs).
Labor Shortages Continue in 2022
The ongoing lack of skilled and unskilled construction workers makes it difficult for builders to stay on schedule and within budget. According to the Commercial Construction Index Q4 2021, 91 percent of contractors reported problems finding skilled workers, and 45 percent reported turning down work due to skilled labor shortages.
The Bureau of Labor Statistics reported 345,000 unfilled construction positions in November 2021, following a record high of 445,000 open jobs in October 2021, significantly higher than the 261,000 a year ago. Consequently, builders, developers, and communities are struggling to start new projects or complete jobs on time due to a lack of workers.
The Growing Need for Construction Workers
The BLS predicts a 6 percent growth (400,000 new jobs) in construction and extraction occupations, with a medium annual wage of $48,610. Additionally, the infrastructure bill will potentially create up to 800,000 jobs in the fourth quarter of 2025.
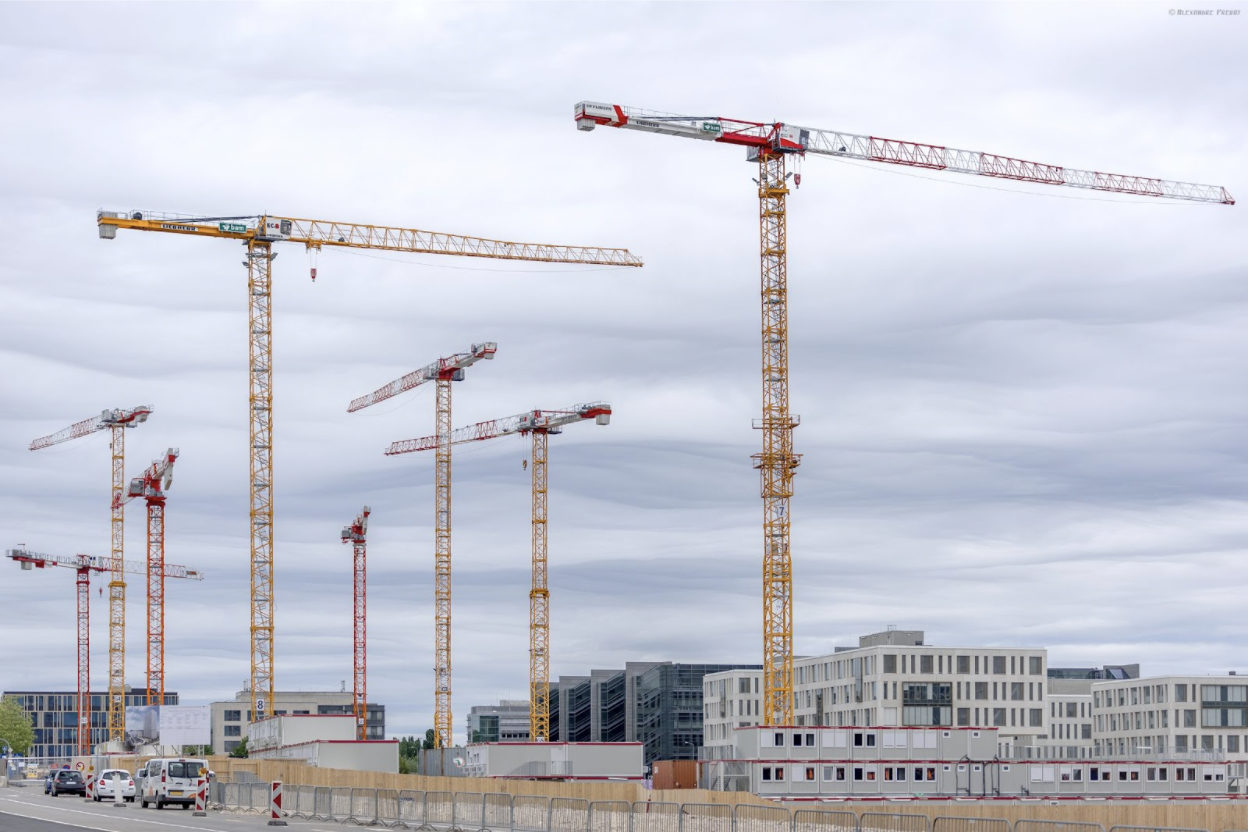
What is Causing the Labor Shortage?
The construction labor shortage began when 600,000 skilled workers left their jobs during the 2008 recession and never returned. The deficit continued to grow with retiring baby boomers and COVID-19. In addition, younger workers believe four-year college will provide a better future over technical trades. However, after graduating, many find the opposite to be true. Skilled labor jobs offer several significant benefits over a college education:
Less education to pay for
Thousands of good-paying job openings
Life-long job skills with long-term opportunities
Supply Chain Woes in 2022
Volatile prices and availability of construction materials due to supply chain issues caused by the pandemic have created incredibly long lead times, making it challenging to estimate project costs accurately. According to the 2021 Q4 Commercial Construction Index, 60 percent of contractors reported the lack of building products as a top consequence of the COVID-19 pandemic, second only to worker shortage (52 percent).
The pandemic strained supply chains and production due to employee absenteeism, closures in manufacturing and distribution centers, and inconsistent suppliers. As a result, building materials prices increased 12.2 percent in 2021, after rising 4.5 percent over the same period in 2020. The increasing prices have driven new home median sales up by 18.8 percent, over the past year, to a record $416,900.
Additionally, current supply chain issues are preventing the startup construction of 152,000 authorized single-family units — up 40.7 percent from a year ago.
Unfortunately, in the U.S., building products and material supply chain challenges may take longer than expected to normalize, limiting contractors' and developers' ability to fully benefit from the current demand for construction and infrastructure money.
Fox Blocks Insulated Concrete Forms (ICFs) Can Alleviate Supply Chain Woes and Labor Shortages
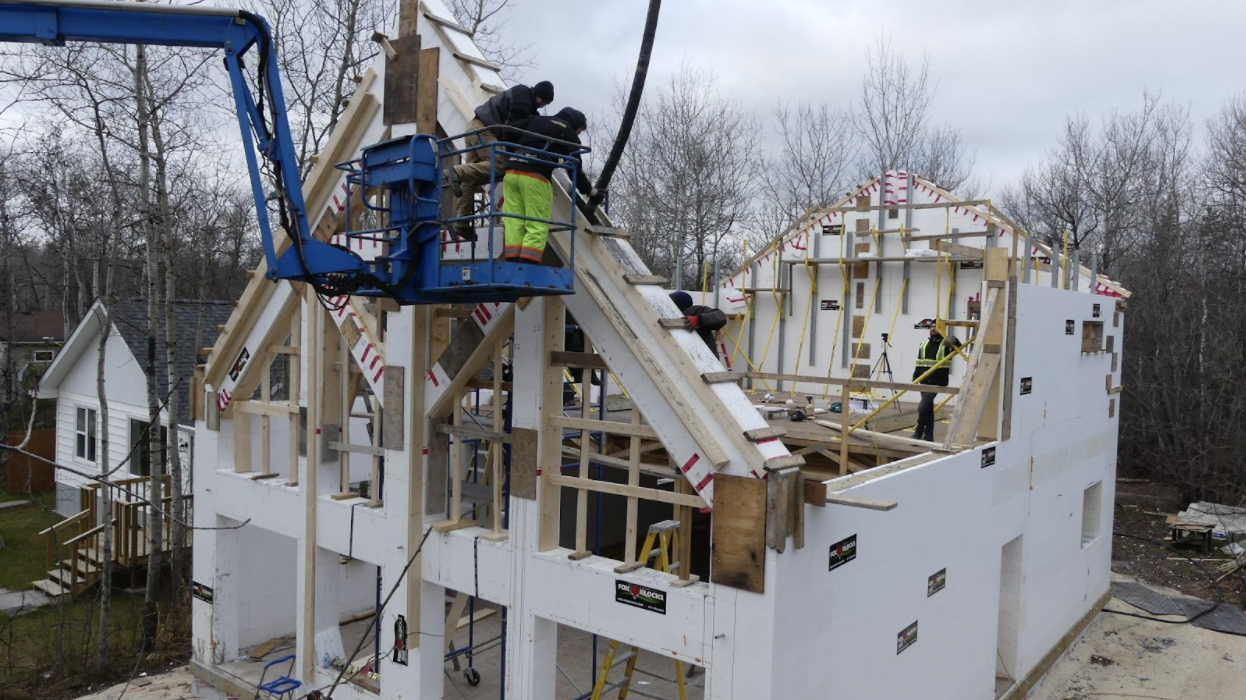
Fox Blocks ICFs provide the construction industry with a solution to the ongoing labor shortages and supply chain problems: modular construction, innovative and cost-efficient material, and an extensive BIM library.
Fox Blocks' modular construction offers all-in-one above- and below-grade wall systems, combining six steps into one: structure, insulation, weather resistant barrier, air barrier, vapor retardant and attachment, to reduce labor needs, and expedite completion timelines. ICF creates energy-efficient, disaster-resistant, durable, and healthy structures without added materials or subcontractors.
Fox Blocks give architects, builders, and developers a cost-effective and available method of building walls and foundations that lessen material needs and waste compared to high-priced wood- and steel.
The Fox Blocks website offers builders and architects a complete resource CAD and BIM library on the product line, code evaluations, testing, and building science attributes to expedite the design and build process. BIM minimizes C and D waste, material requirements, and cost overruns by improving the quality and accuracy of design and construction. BIM can give an overview of your current supply chain, identifying your inefficiencies in under or over-ordering in order to help you to estimate material costs more accurately.
Fox Blocks as an insulated concrete form allows construction to proceed in cold weather versus other traditional building assemblies.
Don't hesitate to contact Fox Blocks professionals today to learn more about what you can do to adapt to supply chain woes and the lack of skilled and unskilled labor.