
A Look at the Rising Cost of Lumber in Home Building

Lumber shortages and skyrocketing prices, mainly from a slowdown at the lumber mills due to the COVID-19 pandemic, are challenging builders to stay on schedule (and budget) while meeting the needs of a booming housing market. Pre-pandemic (February 2020) lumber prices were $455 USD/1000 board feet. After COVID-19, prices briefly dropped to a low of $250; however, costs rapidly increased, reaching a historical high in September 2020 of $930. Unfortunately, experts predict this trend to continue through 2020, at which time lumber costs may start to come down.
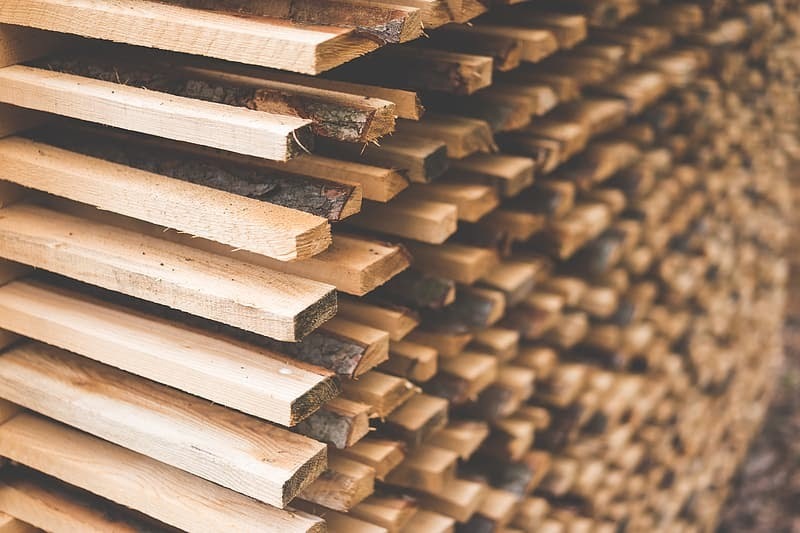
Much of the blame for lumber shortages and high prices lies with the mill slowdowns and closures in April 2020, since mill owners anticipated a decline in the demand for lumber due to COVID-19. However, the opposite happened — possibly due to historically low mortgage interest rates and a low inventory of homes. The current housing starts are at a 10-year high of 1,496,000. Also, tariffs, mill production disruptions due to hurricanes, and an escalation of DIY projects have contributed to the lumber shortages and price increases. The high cost and lack of lumber threaten to slow home construction momentum and lower profit margins for builders.
Declining Lumber Imports Contribute to Shortages
Declining lumber imports further contribute to the lumber shortage. The Monthly U.S. International Trade In Goods and Services, June 2020, from the Census Bureau and Bureau of Economic Analysis reports that U.S. imports of lumber are down by $26 million (year to date). Primary reasons for the decline in lumber imports point to a slowdown at Canadian mills, constraints on border crossings, and U.S. tariffs on Canadian wood (21 percent). Imported wood represents a third of the wood used in construction, with 90.1 percent of it coming from Canada. A reduction in imported wood from Canada has contributed to the lumber shortage and the rising cost of home building in the U.S.
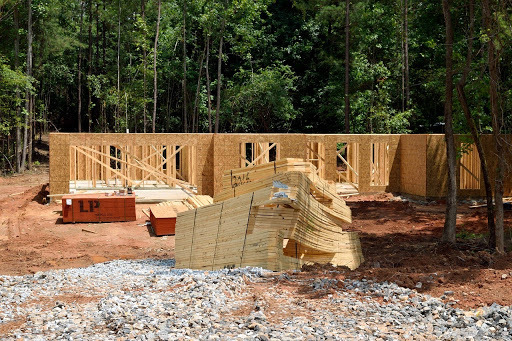
Why Can't the Mills Ramp Up Production?
According to Buck Vandersteen, executive director of the Louisiana Forestry Association, several reasons have caused the mills' slow response to meet the current demand for lumber. Many mill workers furloughed in April found new jobs, making it difficult for mills to fill positions at their facilities. Also, some mills have chosen to stay closed due to continued economic instability. It can take several million dollars to restart a mill, so even with the high price of lumber, controlling the virus must happen before mills can commit to reopening.

Fox Blocks ICF System Offers a Solution to the Rising Costs of Lumber
Framing lumber makes up about a fifth of the material cost of building a home; therefore, contractors that want to avoid lumber's rising and volatile prices should consider an alternative wall system like Fox Blocks insulated concrete forms (ICFs).
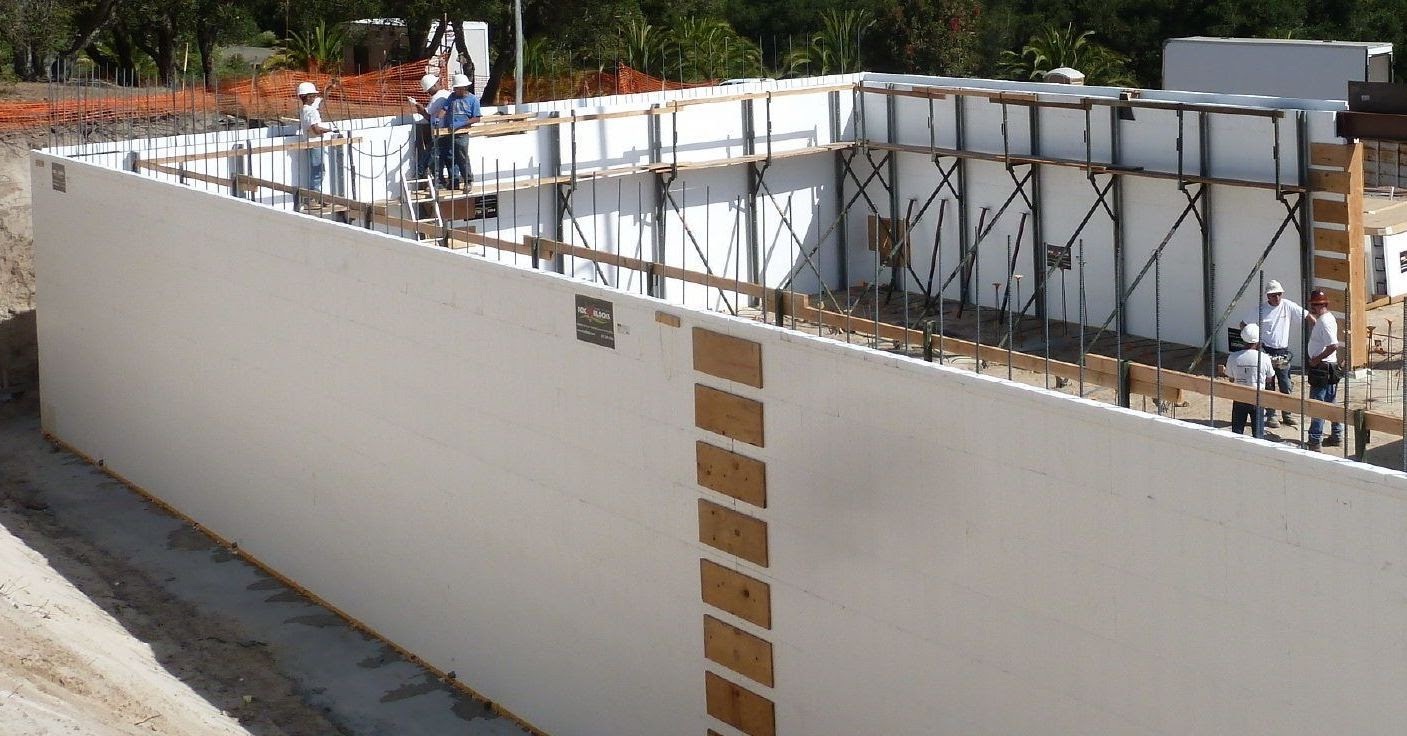
Quick and easy to install, the Fox Blocks ICF wall assembly offers stable and consistent pricing over comparable wood-frame construction. Fox Blocks ICFs create more disaster-, fire-, insect-, and moisture-resistant houses than wood-frame. ICFs also produce a more energy-efficient, noise-reducing, and healthy home than wood. Contractors can avoid the rising costs and shortages of lumber and build a high-performing, safe, and healthy home by choosing Fox Blocks ICF.
Why the Rising Lumber Costs Should Prompt Builders to Use ICF Wall Systems
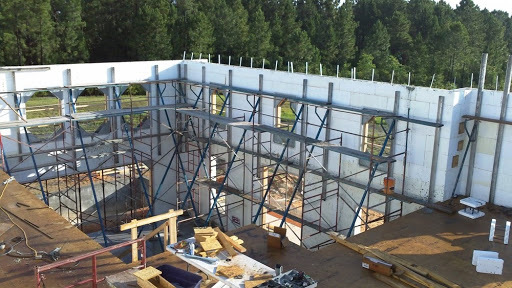
A slowdown at the lumber mills due to the COVID-19 pandemic, combined with other factors, has led to lumber shortages and skyrocketing prices. Consequently, the cost to build a new single-family, wood-framed home has increased by more than $16,000.
Before COVID, the cost of Fox Blocks ICF construction was in line with high-performance wood-framed construction. However, since the pandemic, wood building costs and labor have skyrocketed, making it advantageous to build with ICF and Fox Blocks. ICF construction cost has remained steady throughout COVID because the price of ready-mix concrete has remained steady, and the increasing cost of labor does not affect easy and fast to install ICF as much wood.
Please contact Fox Blocks professionals for more information on how builders and homeowners can avoid lumber's rising costs with ICF during this unprecedented pandemic.