
Reaching the Tipping Point — ICF vs. Wood Framing

For many builders, the lumber and labor shortages have significantly affected their ability to meet schedules, leading to extended completion dates and cost overruns. Perhaps these ongoing challenges represent a tipping point for construction, making us rethink how we do business, starting with whether wood-frame construction remains a cost-effective building method.
Have We Reached a Tipping Point on Construction Methodology?
The ongoing growth of the housing market offers builders an excellent opportunity to grow their businesses. However, the high price and shortages of lumber and labor continue to challenge builders to stay on schedule and budget. In response, contractors must rethink their building methods, particularly when it comes to wood construction.
Have we reached a tipping point where we should move away from wood and towards less cost-volatile products, like Insulated Concrete Form (ICF) construction? Yes. ICF construction is a cost-effective building method that doesn't rely on wood, and it requires less labor to install. ICF also creates energy-efficient, disaster-resistant, and durable structures, all vital features for today's homes and buildings. Contractors planning to take advantage of the home building boom must turn to innovative, alternative building methods, like ICF.
Low Housing Inventory Leads to Housing Boom
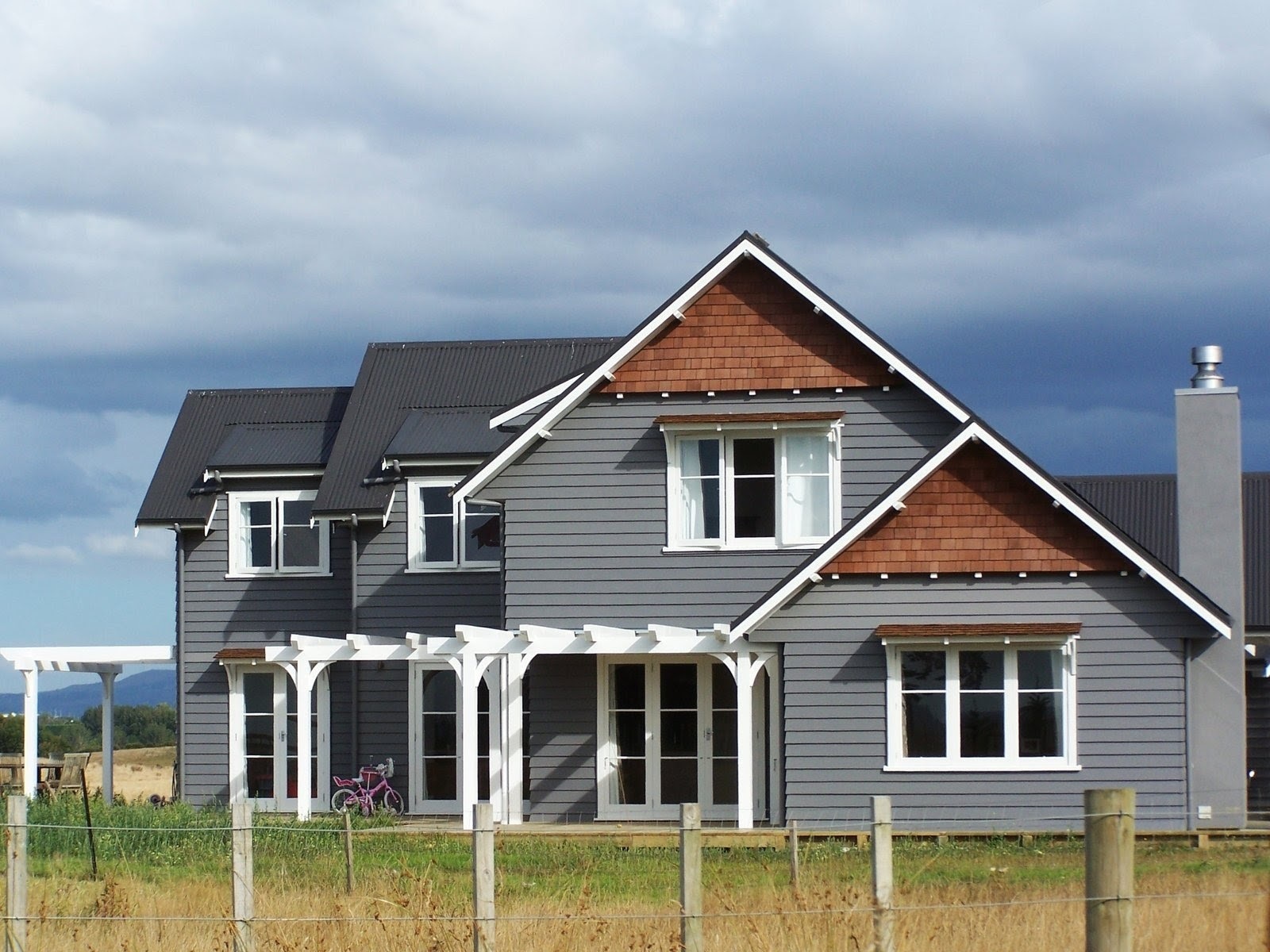
America desperately needs the current home building boom to make up for the considerable lack of housing. For the past ten years, the demand for housing has significantly outweighed the availability of homes for sale, creating a crisis, particularly when it comes to affordable housing. Zillow reports a record low of available homes for sale in February 2021. The low inventory leads to multiple people bidding on the same house, often triggering price increases. Between March and February of 2021, home values surged 1.2 percent – the most monthly increase on record.
The tremendous need for housing has resulted in new home sales soaring 20.7 percent between February and March 2021, reaching the highest level since August 2006. A trend the Mortgage Bankers Association (MBA) forecasts will continue. MBA predicts an increase in single-family housing starts of 1.134 million in 2021, 1.165 million in 2022, and 1.210 million in 2023. The last time single-family housing starts broke 1 million (1.046 million) was in 2007.
Ongoing Problems Facing the Construction Industry
Two significant problems within the construction industry threaten to hamper the home building boom by keeping building costs high and disrupting scheduling: increasing lumber prices and skilled labor shortages.
Lumber Shortages and Escalating Costs
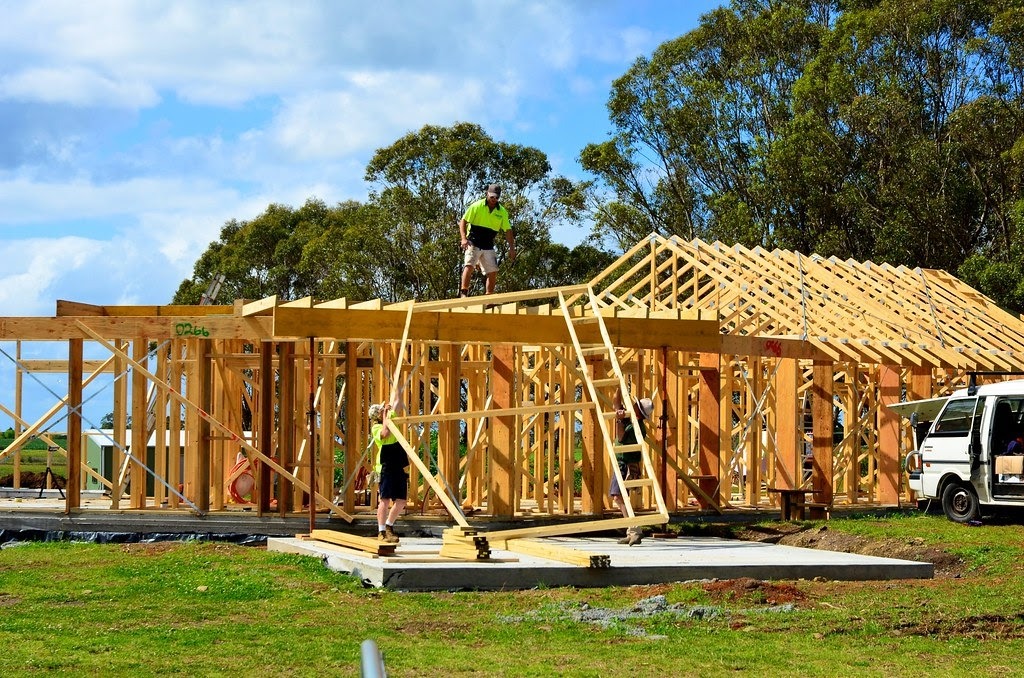
Over the past few years, several situations have caused lumber shortages and increasing costs, spiking the price to over 200 percent. Unfortunately, experts forecast lumber prices to continue to grow through 2021, further increasing construction costs and hampering building starts.
At the start of COVID-19, lumber mills slowed or closed, anticipating a decline in the demand for lumber. However, the opposite happened — home starts increased due to low mortgage interest rates, a low inventory of homes, and home remodeling surges.
The 2020 severe wildfires destroyed 15 billion board feet – enough wood to build 1 million houses.
The 2017 tariffs on Candian softwood lumber imports further contributed to the lumber shortage.
Construction Labor Shortages
Many contractors report turning down work and putting in higher bids due to a lack of skilled construction workers, which is much attributed to workers leaving the field during the great recession, a slowdown in immigration, and low recruitment of younger workers. Contractors report moderate to high levels of difficulty finding skilled workers, with a large percentage saying they have concerns about the workers having adequate skill levels which, in turn, influences the quality of the build.
Many contractors have increased pay and work hours to accommodate the shortages. The average hourly earnings of construction workers reached itshighest level on record in January 2021 ($32.11). At the same time, the average weekly hours worked rose to its highest level since 2019’s third quarter. In 2021, labor costs are predicted to increase 2 percent and 5 percent, further increasing building costs. Nevertheless, contractors plan to employ more people to accommodate the booming housing market than they did one year ago.
Reaching the Tipping Point — ICF vs. Wood Framing
Architects and builders can avoid increasing lumber costs and combat labor shortages by designing new buildings with Fox Blocks ICFs instead of wood. ICFs meet today’s demands for energy-efficient, disaster-resistant design. ICFs have proven record for durability, resiliency, with healthy, comfortable indoor building design features that all add to long-term savings and improved resale value.
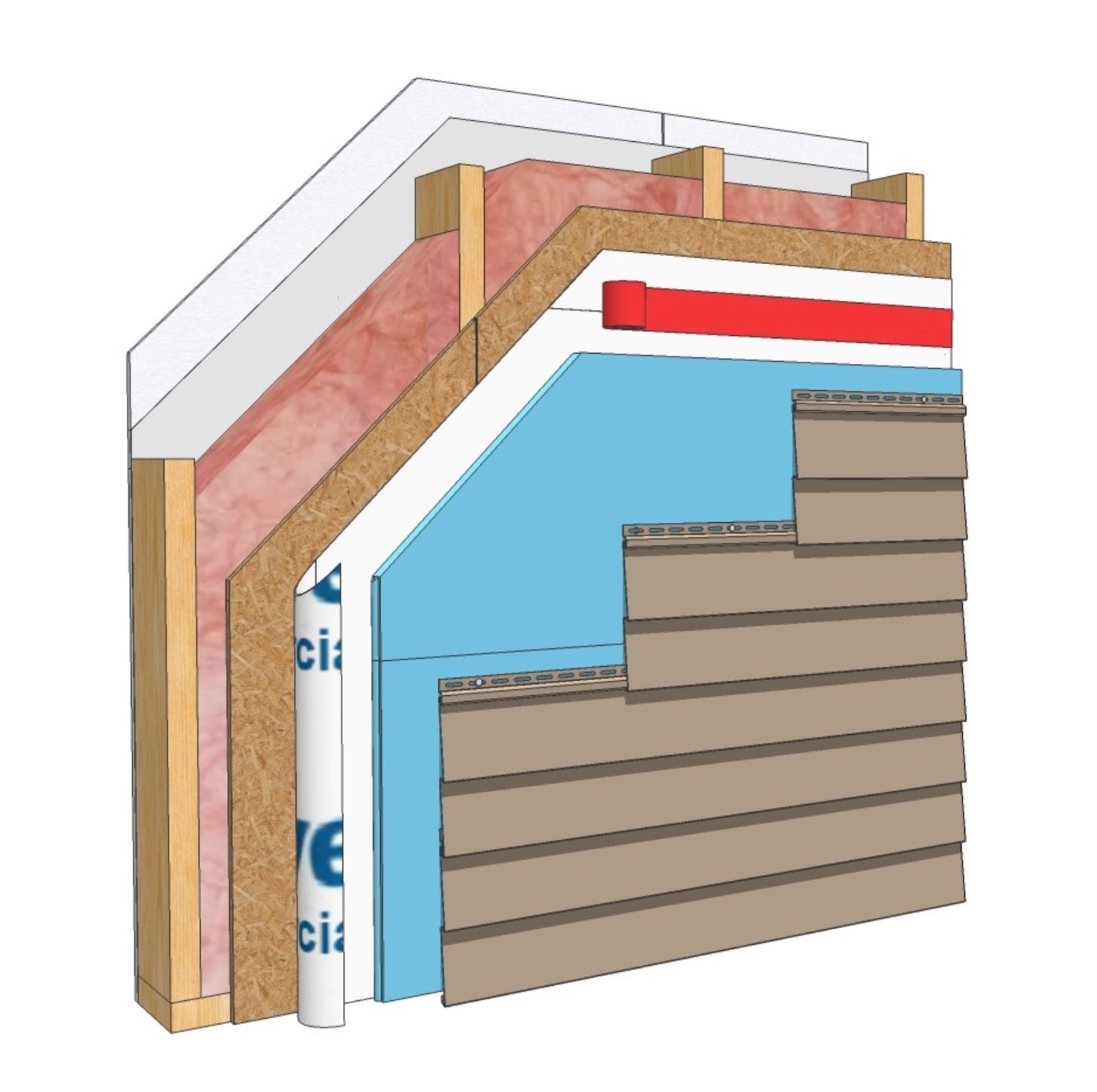
How to Avoid the High Cost of Lumber with Fox Blocks ICF
For over 100 years, builders have used wood-frame construction for both residential and commercial construction. In 2019, builders used wood for 90% of their new homes. However, rising building material costs, added materials for wood wall assemblies to meet minimum codes, and labor shortages may pose the tipping point for builders and architects to switch from wood to Insulated Concrete Form (ICF) construction.
Before rising lumber costs and construction labor shortages, several studies determined that ICF construction would add about 3 to 5 percent to the purchase price of a typical wood-frame home, which amounts to $9,000 to $15.000 for a new home valued at $300,000.
However, with the extreme increases in lumber, this figure no longer applies. Today, you will pay $36,000 more for an average new single-family wood-framed home and nearly $13,000 for a multifamily home than April 2020 prices.
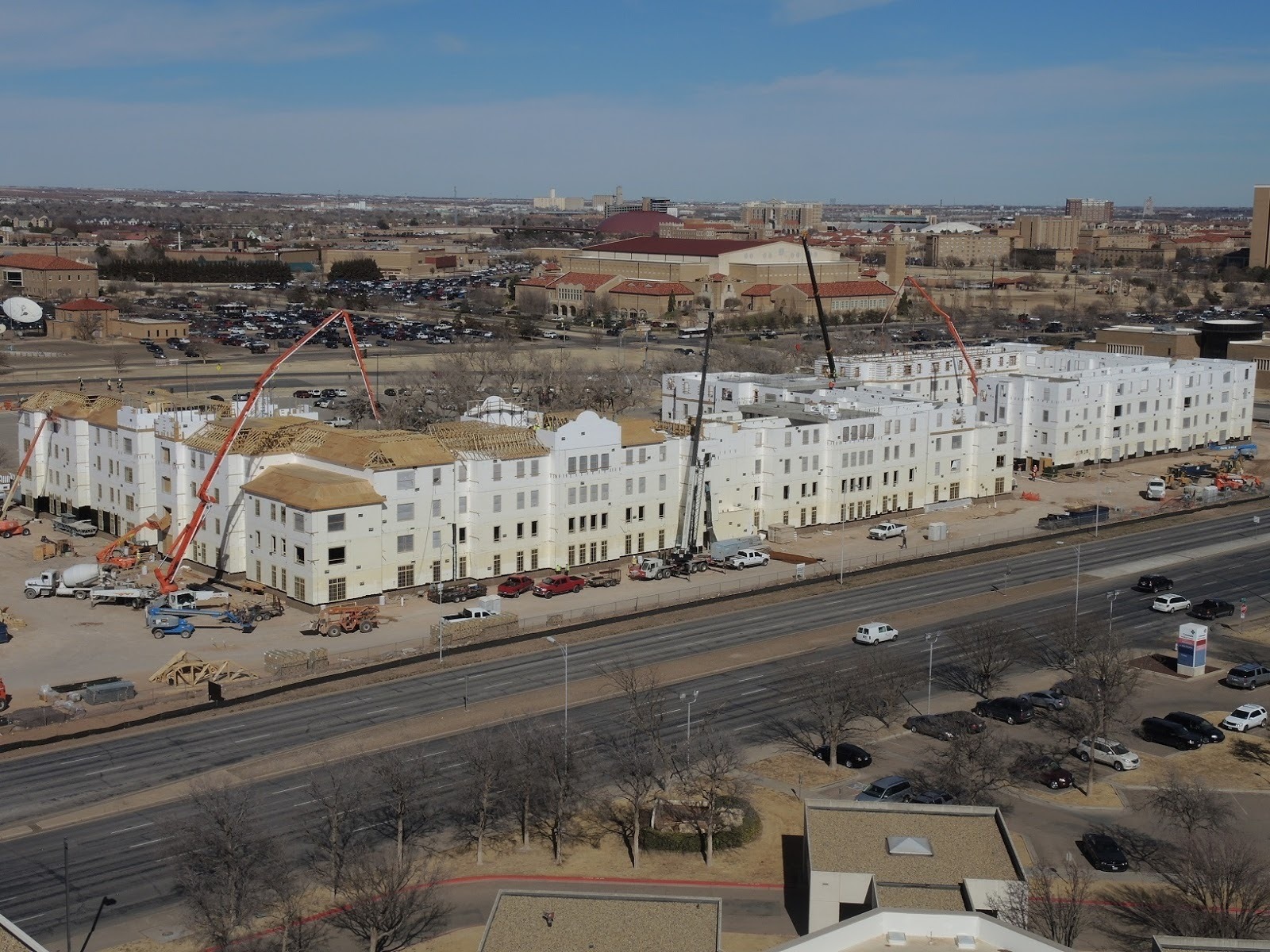
How to Combat Labor Shortages with Fox Blocks ICF
Quick and easy-to-install ICF wall systems limit the need for many of the skilled tradesmen or women required for wood construction. The Fox Blocks all-in-one wall assembly combines five steps into one, including structure, insulation, air barrier, vapor retarder, and attachment. The wall assembly requires less skilled labor than wood framing and hastens project completion time by minimizing the need to coordinate multiple trades to
install insulation on the envelope's interior,
frame exterior walls,
finish framing the foundation wall's interior,
remove the concrete forms, and
apply the poly vapor barrier.
In addition, Fox Blocks ICFs alleviate risk management because fewer workers mean less chance of job site injury.
The Advantages of ICF Instead of Wood-Frame Construction
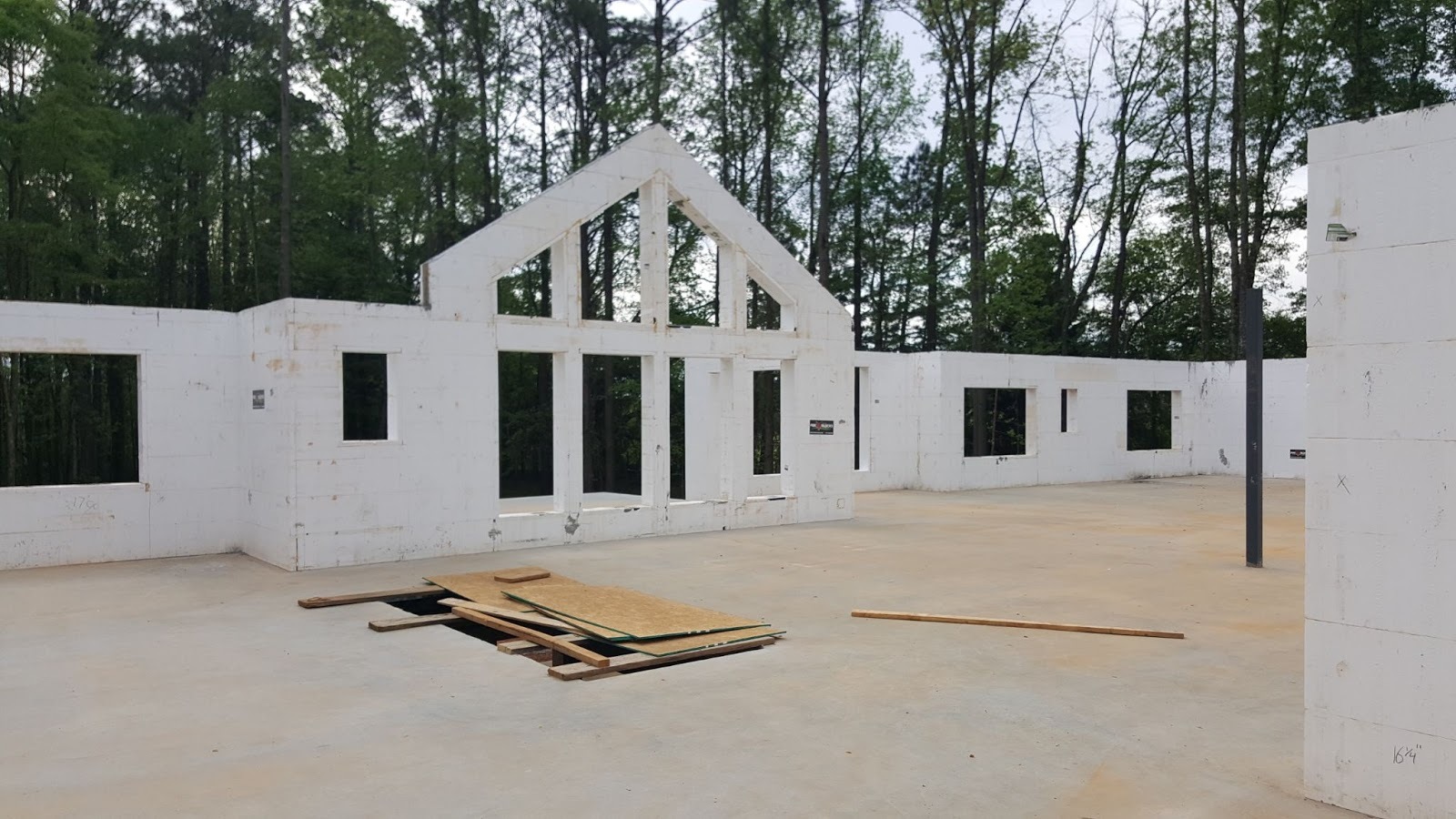
Building an Energy-Efficient Structure: Wood vs. ICF
Low thermal-mass wood creates less energy-efficient structures than those constructed with high-thermal-mass and energy-efficient Fox Blocks, with an R-value of 23 that exceeds ASHRAE/ANSI 90.1 energy code requirements. ICF homes exterior walls require 44 percent less energy to heat and 32 percent less energy to cool and than similar wood-framed homes.
Disaster-Resistant Design
Designing wood-framed houses with the strength to resist severe wind events, flooding, and earthquakes can cost 25–30 percent more than standard construction. Disaster-resistant Fox Blocks ICFs, with steel-reinforced concrete, provide significant strength against severe winds exceeding 200 mph and projectile debris traveling over 100 mph.
Durable Construction
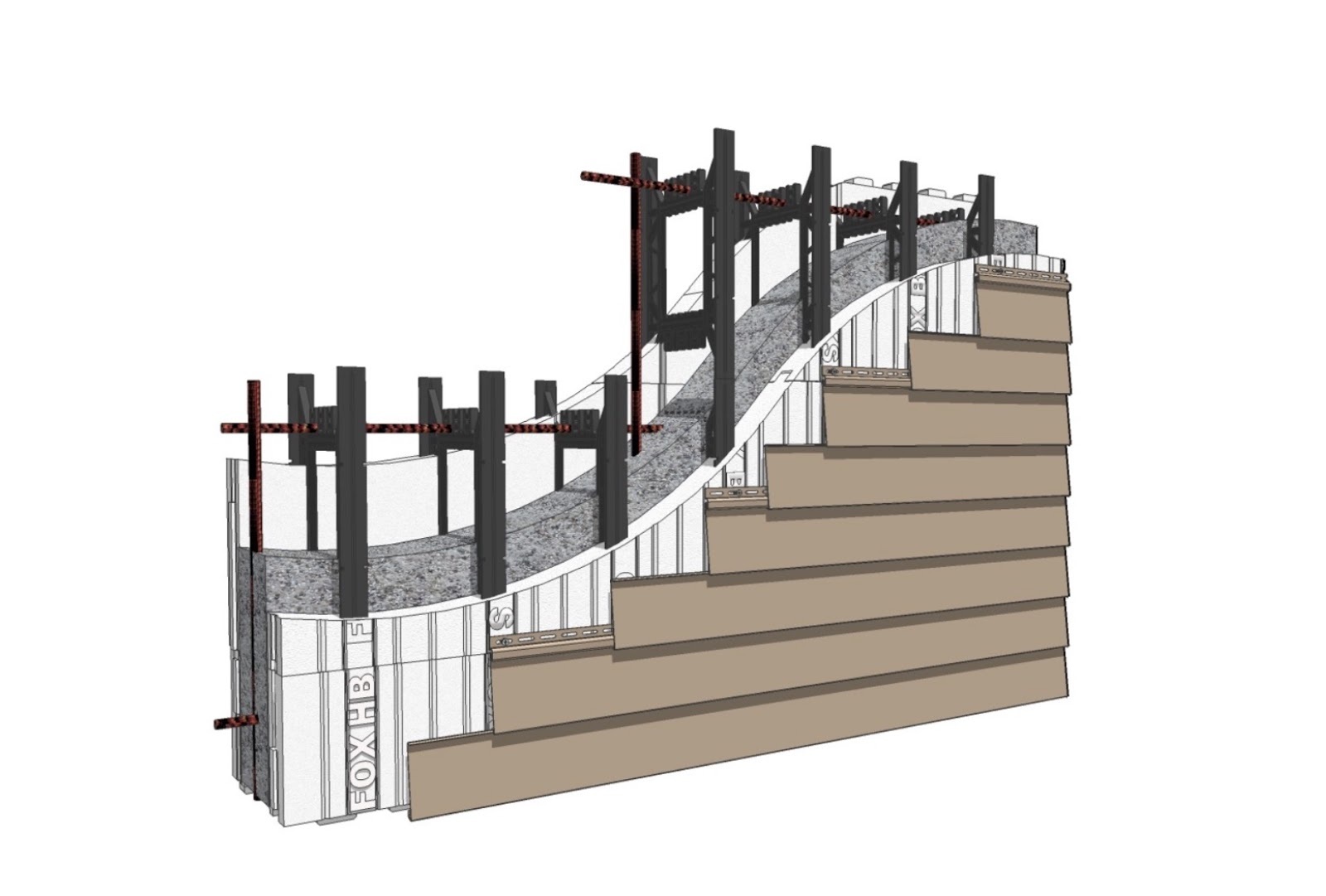
The vulnerability of wood to moisture can lead to unhealthy mold and costly repairs. Also, termite invasion can damage a wood home's durability and cost hundreds, if not thousands of dollars in maintenance and repairs.
Moisture-resistant Fox Block ICFs create a solid continuous monolithic concrete wall with a perm rating below 1.0, controlling moisture intrusion and prohibiting the growth of mold, mildew, and rot. They lack organic material, which pests such as termites like to eat. Fox Blocks recommends Polyguard Products, Inc. 650 XTM or 650 XTP membranes for termite and waterproofing protection for the all-in-one wall system.
How Fox Blocks ICF Is a Solution to Rising Lumber Costs and Ongoing Labor Shortages
In today’s construction market, the scales have reached the tipping point away from wood and towards ICFs. The cost of building ICF structures and availability of Fox Blocks should prompt contractors to switch from wood construction to Fox Blocks ICF. Fox Blocks provide a resilient, secure, reinforced concrete wall assembly for any home or building. ICFs also eliminate the need for expensive lumber. Fox Blocks ICF also helps contractors to hasten completion times and limit callbacks, compared to wood frame construction.
Fox Blocks ICF Training
Fox Blocks makes the transition from wood to ICF easy with online training on the Fox Blocks Integrated Learning Center website, technical documentation available for review on the main website Resources, and the Estimator Pro material and labor estimating program.
It’s easy to find Fox Blocks products through building supply outlets.
Our experience shows that once a contractor switches to ICFs for below and above-ground wall systems, the simplicity and quickness of its installation make them stop framing exterior walls with wood. ICF also helps contractors expand their scope of work and profit margins.
Please contact the Fox Block professionals today to find out about more advantages of ICF over wood construction.