
How to Build an Apartment Complex Faster (and Better)

The demand for high-quality, multi-family residential spaces has never been higher. Developers are constantly on the lookout for innovative strategies and construction technologies to expedite the building process without compromising on quality. Most metropolitan areas report apartment occupancy rates of 93% or higher.
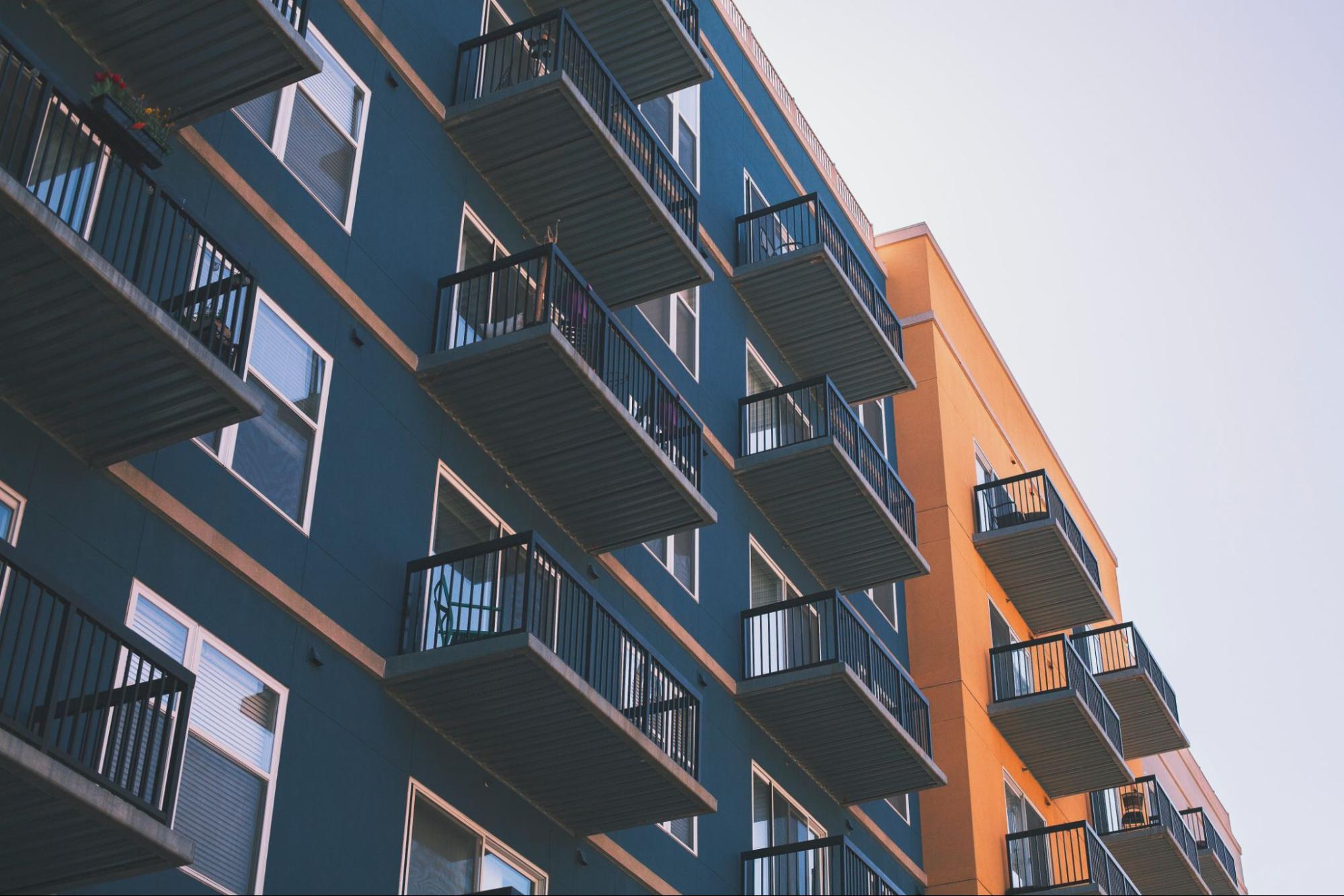
With such strong and growing demand, the race is on to meet that demand. One question often asked when discussing building apartment complexes is, "How long does it take to actually build an apartment complex?" The answer varies depending on various factors, but with the right construction process and materials, it can be significantly faster than you might think.
The Traditional Apartment Building Construction Process
The conventional method of apartment building construction involves a lot of manual labor and materials such as softwood lumber, masonry blocks, structural steel. The process can take anywhere from a year to a few years, depending on the size and complexity of the project. Before any construction can begin, plans must be produced and permits must be obtained. Once all of the administrative work is out of the way, the clock starts for getting the apartment complex built.
Many construction techniques require massive amounts of labor to build these structures. Factors such as weather, availability of materials, and labor can further extend the construction timeline. Experienced crews and contractors are also able to accomplish projects faster than more novice crews.
Accelerating Construction with Modern Techniques
In the quest to find ways to build apartments faster, developers have turned to modern construction techniques that often streamline projects and reduce labor requirements.
Prefabricated units and modular construction have garnered a lot of attention lately due to their speed and efficiency. However, there's another innovative solution that's rapidly gaining popularity - the use of insulated concrete forms (ICFs).
Building Faster with Insulated Concrete Forms
Insulated Concrete Forms are interlocking modular units consisting of two sheets of polystyrene foam held together with ties. The lightweight blocks are dry-stacked on site to form the building’s features. Steel reinforcing bars are then placed in the hollow cavity between the foam sheets. Finally, the walls are filled with concrete and allowed to set.
Once the concrete cures, the resulting steel-reinforced concrete structure is ready to provide tremendous strength to the building. The walls also have built-in continuous layers of both interior and exterior insulation. The forms serve as a permanent interior and exterior substrate for all typical finishes as well, and provide the bearing support for floors and roofs which significantly speeds up the apartment building construction process.
How long does it take to build an apartment complex using ICFs? Thanks to the streamlined construction process, a complex that would traditionally take a year to construct can potentially be finished in 9-10 months.
Benefits of Using ICFs in Apartment Building Construction
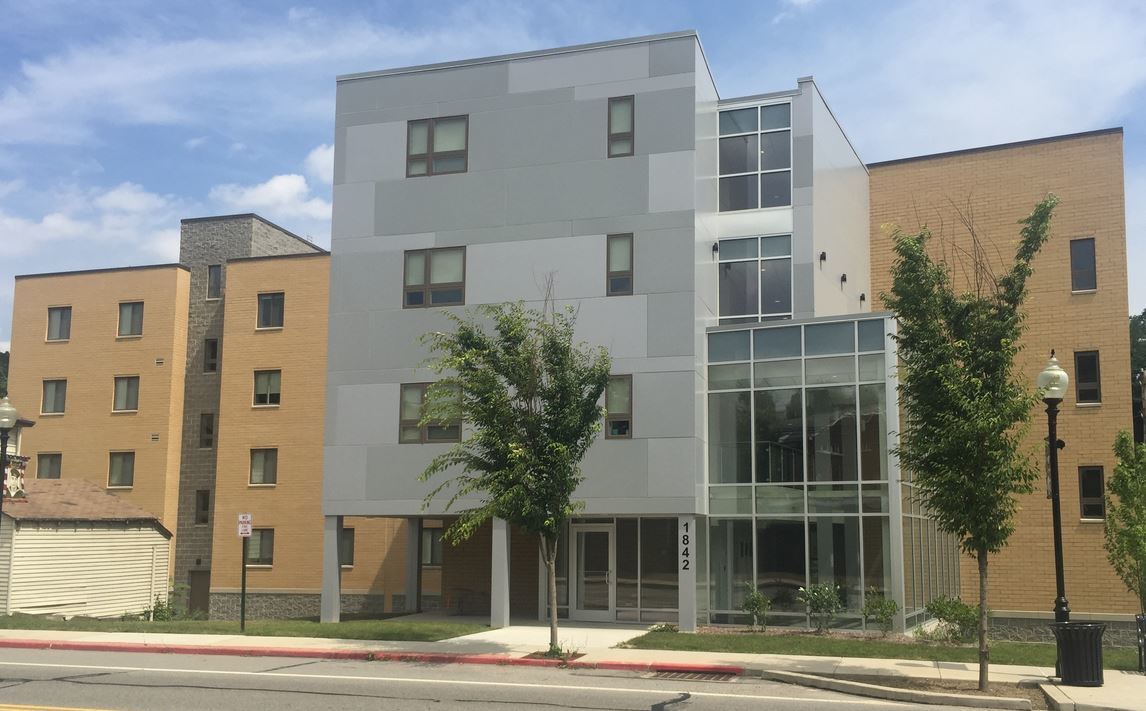
Beyond speed, there are several other benefits to using ICFs for apartment building construction:
Energy Efficiency
ICFs have superior insulation properties, for substantial energy savings compared to traditional construction methods. This is a selling point for environmentally conscious renters and helps keep utility costs low. The enhanced energy efficiency can also help reduce the size and cost of the building’s HVAC equipment, to reduce the total capital expenditure required.
Strength and Durability
ICFs provide superior strength and resistance to natural disasters, including hurricanes, tornadoes, and earthquakes. ICF blocks are so strong they are often used to build tornado safe houses. This resilience translates to less maintenance and long-term cost savings. ICF buildings are also low-maintenance which keeps operating expenses at a minimum.
Noise Reduction
The insulation properties of ICFs also provide excellent soundproofing, a valuable feature in multi-family housing. ICF blocks have top-of-class sound transmission classifications, which makes them an easy choice for buildings where noise is a concern especially for interior demising walls between units.
Flexibility in Design
Despite their strength, ICFs are flexible for design and come in many shapes, to allow for unique architectural designs and customization. ICF construction gives architects and designers options that they may not have had otherwise.
Environmentally Friendly
ICFs contribute to a sustainable construction process by minimizing waste and reducing the reliance on natural resources. ICF blocks often contain up to 48% recycled material by weight. Also, the concrete used in ICF construction is typically sourced locally.
The Future of Apartment Building Construction
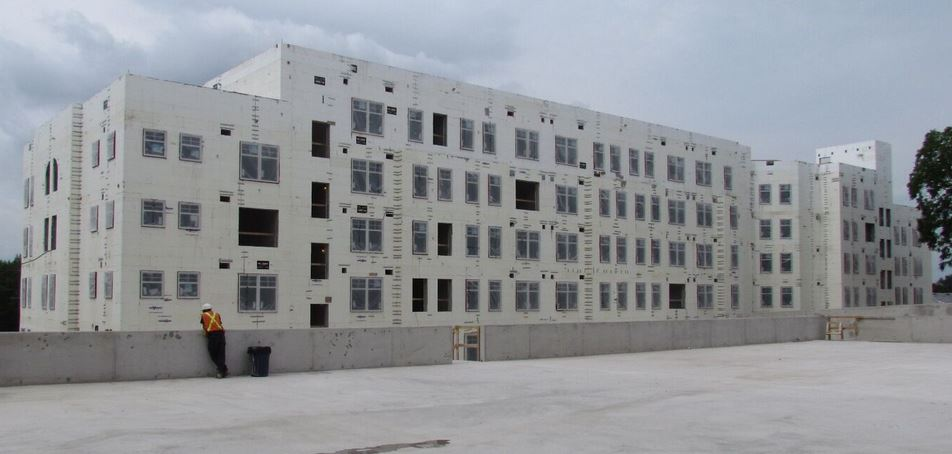
The future of apartment building construction lies in leveraging innovative materials and processes to deliver better projects faster and more efficiently. Insulated concrete forms are at the forefront of this revolution, and provide a compelling answer to the question, how can an apartment complex be built quickly and efficiently.
If you're a developer or builder looking for ways to accelerate your apartment building construction process, ICFs are a proven, efficient, and cost-effective solution.
Fox Blocks provides top-quality ICFs designed to make your construction process faster and more efficient. Their team of experts is ready to assist you in exploring how ICFs can be integrated into your next project.
Don't let your construction timeline drag on longer than necessary. Reach out to the team today to learn more about how you can build apartment complexes faster with Fox Blocks!