
How to Build Medical Office Buildings Faster

In the dynamic world of healthcare, the need for medical facilities, including offices and clinics, is ever-growing. Whether responding to a health crisis or simply accommodating a rapidly expanding local population, speed in construction without compromising quality is critical. This article will discuss various techniques to expedite the construction of medical office buildings.
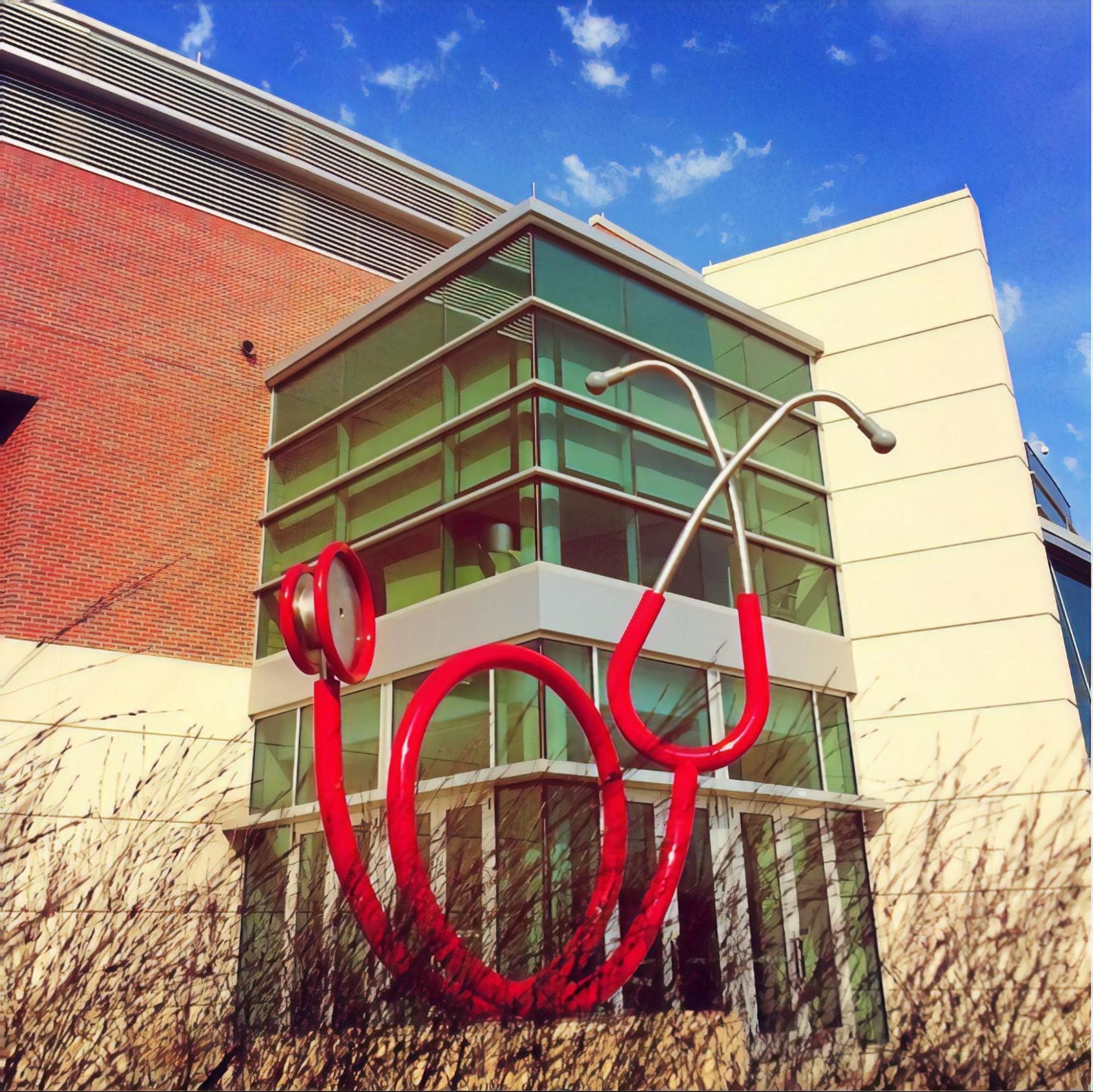
Methods of Construction
Stick Framing – The Traditional Favorite
Stick framing, also known as "platform framing," involves constructing one floor at a time with a repeated process. It utilizes a system of individual studs to erect walls and has been a standard method for decades.
Advantages of Stick Framing
Flexibility: Stick framing doesn’t require large machinery or specialized labor. It allows for on-the-spot design alterations which makes it adaptable.
Availability of Materials: Lumber, the primary material for stick framing, is widely available, which makes it a go-to choice in many regions.
Tried and Tested: Builders and architects are familiar with the nuances of stick framing, so it’s often the default choice. While stick framing has its benefits, it may not always be the fastest, especially when compared to some of the newer techniques available today.
Prefabrication – The First Major Improvement in Construction Practices
One of the time-tested strategies in building structures quickly is the utilization of prefabrication. Prefabrication, often abbreviated as 'prefab', refers to the practice of assembling components, like Mechanical, Electrical, and Plumbing (MEP) elements, off-site in a controlled environment. Once completed, the prefab components are transported to the construction site for integration.
Benefits of Prefab
Time-saving: By pre-assembling components, builders can conduct multiple construction activities in parallel which can dramatically reduce the project's duration.
Quality Assurance: Constructing in a controlled environment ensures a higher degree of precision to help minimize errors.
Cost-efficiency: The predictability in the prefab process can lead to fewer surprises and associated costs.
Insulated Concrete Forms (ICFs) – A New Era of Speed and Efficiency
As construction schedules have become tighter and tighter, Insulated Concrete Forms (ICFs) have emerged as a potential game-changer that involves an unmatched blend of speed, quality, and sustainability.
What Are ICFs?
Insulated Concrete Forms are permanent concrete formwork systems that serve as a structural and insulative solution. They are essentially hollow blocks or panels made of expanded polystyrene foam (EPS) that are stacked into the shape of the exterior walls of a building, reinforced with steel, and then filled with concrete. This method allows a building's structure and insulation to be built at the same time, which significantly reduces construction time.
Why Choose ICFs for Medical Office Building Construction?
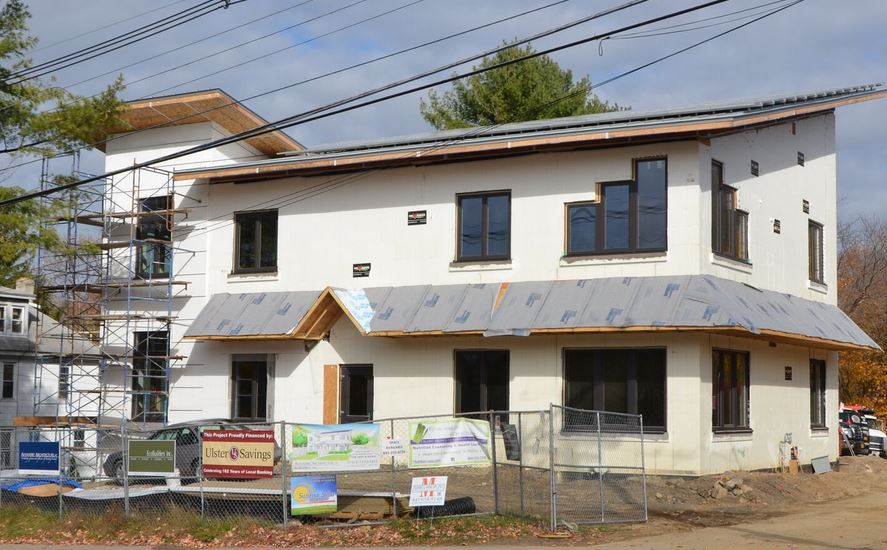
Owners of medical office structures are seeking strategies that go beyond focusing on singular buildings and instead aim for a broader, repeatable framework. Rather than treating the construction of each structure as an isolated project, the trend is leaning towards a systematic, production-line approach. This evolution shows their commitment to improving construction quality, speeding up project timelines, and increasing the overall value of their business. As the building owner operating expenses to maintain the building and the controlled environment are a big concern. ICFs provides a high-performance building which will provide lonn lasting monthly operating cost savings.
Speed of Construction
All-in-One Solution: ICF blocks merge the processes of forming, insulating, and structuring a building. Traditional construction often requires these steps to be done separately, which consumes more time.
Less Labor Intensive: The modular, interlocking design of ICF blocks simplifies the construction process. The straightforward stacking and interlocking system means less specialized labor and fewer tools are needed.
No Stripping of Forms: In traditional concrete construction, after the concrete sets, the forms need to be removed, which is an additional step and requires labor. With ICFs, the forms remain in place and act as insulation, which expedites the building process.
Reduced Material Handling: ICFs combine structure and insulation to reduce the need for multiple materials and the time taken to transport, organize, and handle them.
Streamlined Finishing: The design of ICFs allows for quick application of final finishes, and eliminates the need for preparatory steps like furring strips, which are often required in traditional building methods.
Thermal Efficiency
Continuous Insulation: ICF walls provide continuous insulation without any breaks or gaps, unlike traditional construction methods that can have thermal bridges. The consistent layer of insulation ensures that there are no weak points where heat can escape or enter.
Thermal Mass of Concrete: The concrete core in ICFs acts as a thermal mass that stores and releases energy slowly. This means that during the daytime, the concrete absorbs heat and prevents the interior of the building from becoming too hot. During cooler nights, the stored heat in the concrete is gradually released, which helps to keep the interior warm.
Air Tightness: ICF construction results in a more airtight building envelope that reduces the infiltration of outside air, which can bring in unwanted heat during the summer or cold during the winter. With reduced air leakage, HVAC systems don't have to work as hard, which leads to energy savings.
Reduced Thermal Bridging: In traditional construction, components such as studs or joists can act as thermal bridges, where heat can transfer more readily. ICFs, with their continuous insulation and lack of such structural elements in the insulating layer, significantly reduce the possibility of thermal bridging.
Strength and Durability
The combination of concrete and reinforcement of ICF construction makes the building resistant to natural disasters, an essential trait for medical facilities.
Reinforced Concrete Core: At the heart of ICF is a solid core of reinforced concrete that provides exceptional compressive strength, to help make structures resistant to a wide range of stresses and strains that can compromise other building methods.
Resistance to Natural Disasters: ICF buildings have proven to withstand extreme conditions such as tornadoes, hurricanes, and earthquakes better than many traditionally-built structures. The solid monolithic nature of ICF walls makes them able to resist high wind pressures and the impact from flying debris.
Pest and Mold Resistance: Unlike wood, which can be susceptible to termites and other pests, the concrete core of ICFs does not provide a food source for pests. In addition, the moisture-resistant properties of ICFs reduce the potential for mold growth, to help ensure the longevity of the structure.
Fire Resistance: ICF walls have a high fire resistance rating. The combination of concrete and the foam insulation used in ICFs can resist fire for several hours, which is far longer than many traditional building materials.
In short, the integration of reinforced concrete, coupled with the insulating properties and overall design of ICFs, results in a building method that provides superior strength and durability compared to many standard construction practices.
Soundproofing
The soundproofing qualities of ICF (Insulated Concrete Forms) construction also provides distinct advantages for medical office clinics:
Patient Privacy: Medical consultations often involve the discussion of sensitive and confidential information. The soundproofing nature of ICF walls ensures conversations will remain private, and adhere to patient confidentiality standards, to help ensure patient comfort.
Tranquil Healing Environment: A quiet environment is conducive to healing. Patients recovering or awaiting procedures can benefit from reduced external noise, which helps in reducing stress and anxiety.
Minimized Distractions: For medical professionals, a quiet environment is essential for concentration, especially during diagnostics or delicate procedures. ICF construction ensures that external noises, such as traffic or construction, don't interfere with the tasks at hand.
Versatility in Clinic Design: The soundproofing attributes of ICFs allow for greater flexibility in the clinic's layout. Sensitive areas, such as examination rooms, can be placed adjacent to potentially louder spaces without the concern of noise bleed.
Enhanced Patient Experience: A quieter clinic contributes to a more positive patient experience, which can lead to better patient reviews and higher patient retention rates for the clinic.
Transform Your Approach to Constructing Medical Office Buildings with the Innovative, Time-Saving Solution of Fox Blocks
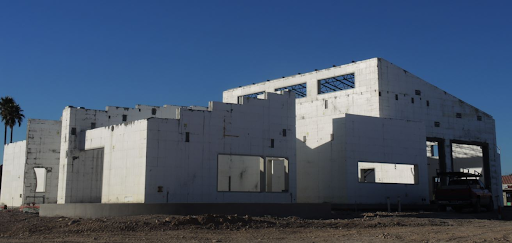
Ready to redefine your approach to constructing medical offices? With Fox Blocks, you can accelerate your construction timeline, reduce labor costs, and create a building that stands the test of time. Plus, our commitment to thermal efficiency, strength, durability, and soundproofing ensures your clinic will offer a comfortable, safe, and private environment for all.
Contact us today to learn more about all of our ICF solutions.