
Foundation Types: 8 Different Types of Home Foundations

A home’s integrity depends significantly on a strong and durable foundation. The right selection of foundation type and material can also improve a construction business’s profitability by saving on labor costs and potential repairs if the foundation fails while still under warranty. Foundation type and material depend on how the homeowner plans to use the space, the local climate, the soil and water conditions, and the site's topography.
The Importance of a House Foundation
A strong foundation shifts a home’s load to the footings and into the ground, resisting seismic and wind forces and providing anchorage for the above-grade building. A durable foundation ensures a moisture-resistant barrier (following the building codes) and resists bending and shear stresses from water and lateral soil pressures. A poorly constructed foundation can lead to tremendous structural damage, endangering the home’s occupants and the neighborhood.
What to Consider When Choosing a Foundation
The foundation type and material must ensure a solid and long-lasting foundation able to support the weight of the house. Elements to consider when choosing the type and material choice for the foundation include:
Use
The foundation type you choose depends on how you plan to use the below-grade space. For instance, if you plan to use it as living or storage space, the foundation’s design should provide a warm, dry, and healthy basement or crawl space.
The Local Climate
Climate affects the foundation choice. For example, in warmer climates prone to termites, you should avoid wood foundations. You should also avoid slab foundations in cold regions with freeze and thaw cycles because the foundation will crack under pressure.
Soil
A foundation requires settled and undisturbed soil to prevent shifts resulting in a breakdown of the house. To ensure that your foundation will perform adequately, conduct a soil test to determine the kind of soil at the site, its moisture content, and its compaction quality.
Moisture
To ensure a long-lasting and robust foundation, you must make sure the foundation will stay dry with a perc test. A perc test determines if the soil will percolate water through it properly for a septic system, keeping the groundwater from accessing the foundation. However, you should still protect the foundation with drainage materials like gutters, downspouts, and a sub-slab drainage pad that redirects moisture away from the foundation.
Topography
The layout of your building lot affects your foundation style. For example, a daylight foundation requires a sloping lot.
8 Types of Home Foundations
Three common house foundation types include basements (30 percent), crawlspaces (15 percent), and concrete slabs (54 percent). Builders can construct basements and crawl spaces with several types of materials: wood, stone, poured concrete, concrete masonry units (CMU), concrete panels, and insulated concrete forms (ICFs).
1. Poured Concrete Slab
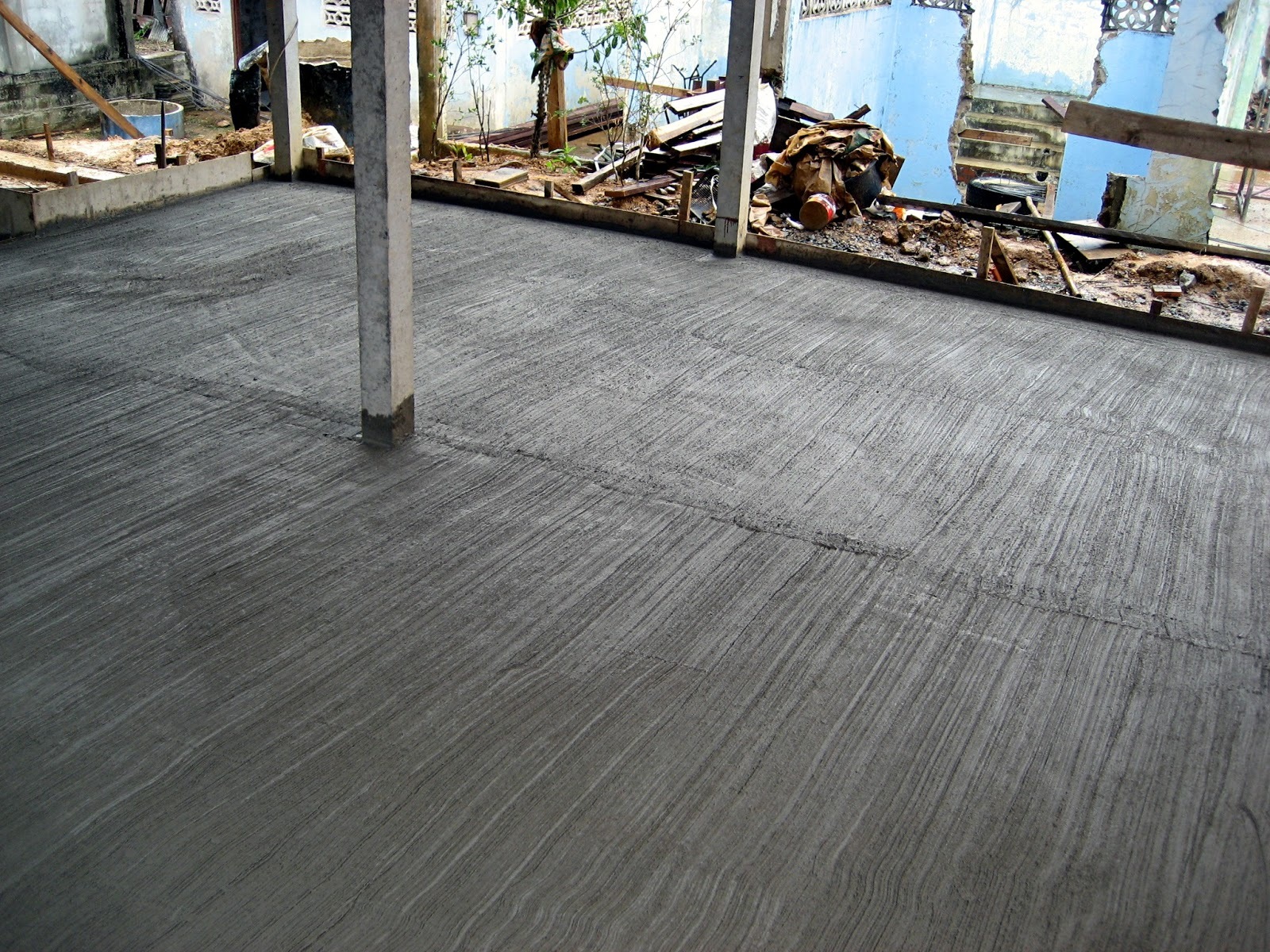
Concrete slab foundations (slab-on-grade foundations) with a thickness of four to eight inches, cost less than basements or crawl spaces. They work best in climates where the ground doesn't freeze and thaw in the winter. However, the home’s water and drainage pipes are difficult to access because they lie just a few inches below the slab.
2. Crawl Space Foundation
Three to four-foot deep crawl spaces are typically unheated but vented for airflow to prevent moisture build-up. Crawl space foundations support the entire structure and provide some storage and possibly enough room for the furnace and water heater. Materials used for crawl space foundation include ICFs, CMUs, and poured concrete walls.
3. Wood Foundation
Building a wood foundation includes below-grade foundation walls made of wood pressure-treated with chromated copper arsenate (CCA) sitting on a concrete slab atop a bed of crushed gravel or rock. The CCA provides resistance to fungus, mold, rot, termites, and ants.
Some consider wood foundations easier and quicker to install, creating warmer homes with lower energy bills than CMUs and poured concrete wall foundations. However, wood foundations cost more than CMUs and poured concrete walls, and are toxic to workers during installation. Moreover, rot and insects can damage a wood foundation if it is not correctly built.
4. Stone
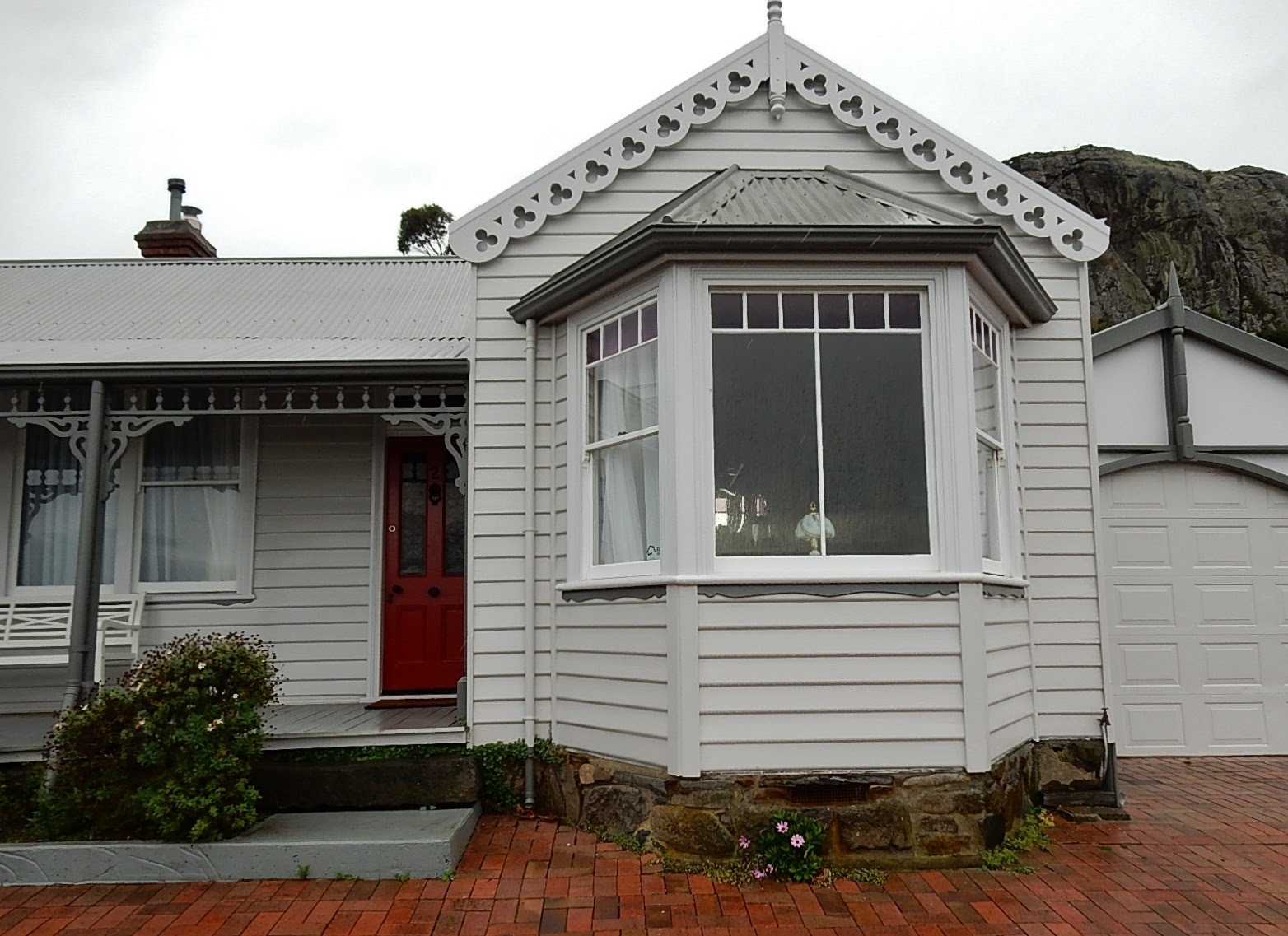
Common during the early 20th century, charming stone foundations contain stones, bound together with mortar spread between the stones and on top. Stone foundations require waterproofing to prevent the mortar from degrading and diminishing the durability and strength of the wall. Also, stone foundations will crack and bow if the house is not level or improperly built, leading to water leakages.
5. Pre-Poured Concrete
The density, strength, and joint-free construction of poured concrete foundations makes them more waterproof than CMU foundations. In addition, poured concrete foundations construct faster than CMU foundations.
However, the strength of poured concrete foundations diminishes if it spalls (when the concrete surface peels, crumbles, or flakes off). Water leakage problems can occur if the wall cracks due to improper construction, non-structural cracks and if the foundation drops, settles, or sinks from the soil, collapsing below the foundation. Moreover, poured concrete foundation, with low R-values of less than 3, offers little insulation value.
The first step in building traditional poured concrete foundations involves constructing and securing large-heavy-wooden form walls for an 8- or 10-inch wall. Next, workers pour concrete continuously into the wooden forms, hardening (cures) onsite—rebar, installed in the footing, secures the weak points and joints.
6. Concrete Masonry Units
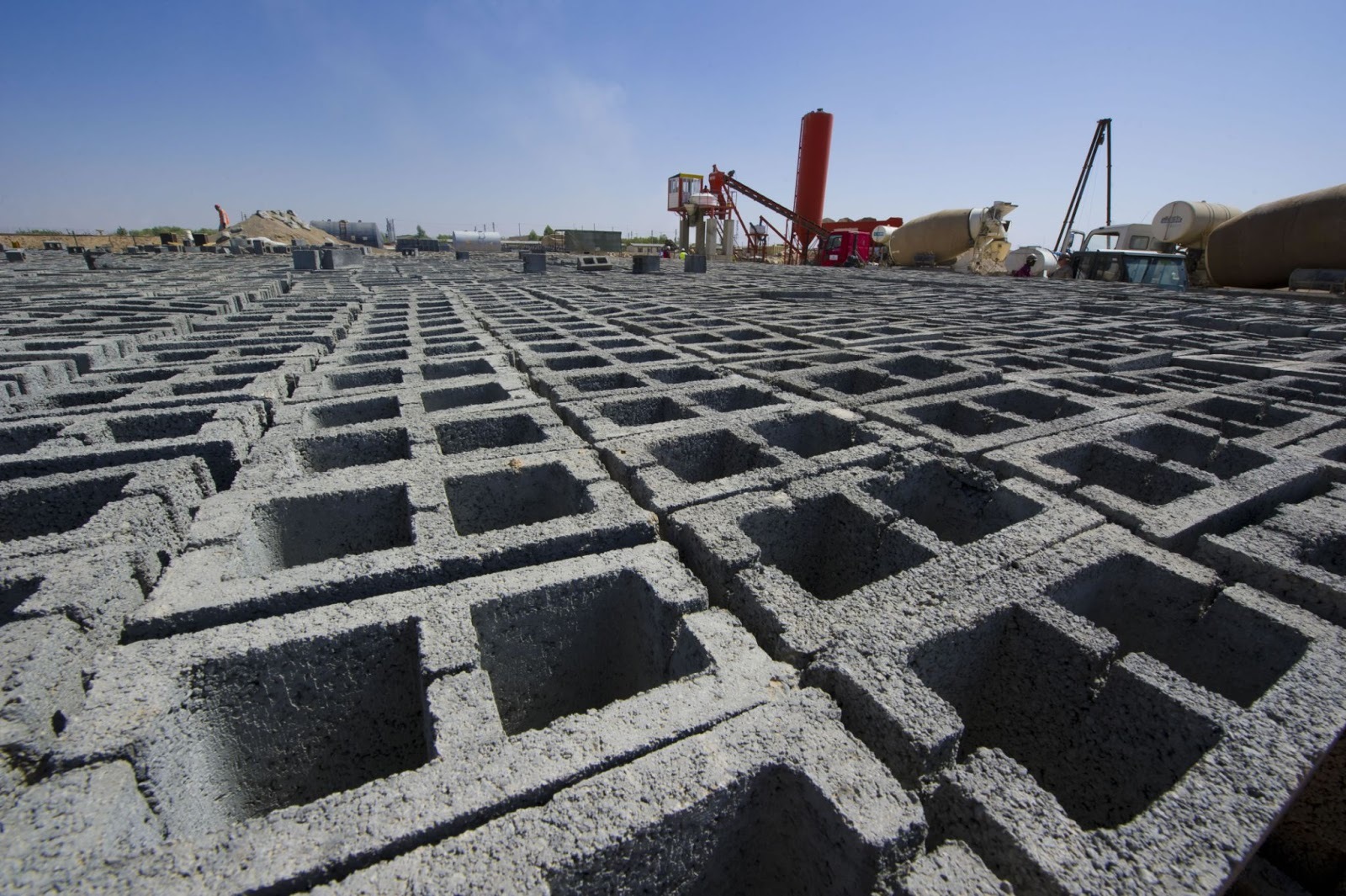
Properly installed CMU foundations provide more compression strength than poured concrete foundations. Installing CMU foundations saves on labor costs because they do not require massive wooden forms, like poured concrete.
However, a CMU wall requires an air and moisture barrier, adding another trade to the foundation product. Water can wear down the mortar holding the CMUs together, diminishing CMU foundations' integrity, resulting in expensive repairs. CMU walls that are not fully grouted with rebar will lose lateral strength. CMU foundations offer little insulation with low R-values ranging from 2 to 3.
CMU foundations often use large (8- or 10-inch wide and 16-inch long) hollow concrete blocks, however sizes can vary depending on the home's weight load. To optimize stability and strength, professionals install the blocks in an overlapping pattern, inserting steel rods vertically and horizontally into the blocks' openings. The blocks rest on concrete footings that are held together with mortar.
7. Concrete Panels
Concrete panel foundations have solid concrete studs for load-bearing support and a concrete footing. Some also include insulation (R-value ≅ 5) and polypropylene fibers and rebar for strength. A precast concrete foundation works best with consistent sill heights of a full basement. Different wall heights slow the building process, lessening the cost benefits.
Concrete panels are prone to moisture problems if improperly detailed, leading to unhealthy and structurally damaging mold. Fire Engineering Magazine reports several fire-related related problems with precast concrete panels.
Constructing a concrete panel basement begins by preparing a gravel base, then placing and connecting the panels, installing a capillary break, and installing the flooring and backfilling. Quick to install concrete panels do not require concrete onsite and can proceed in any weather - freezing or wet.
8. Below-Grade ICF Walls
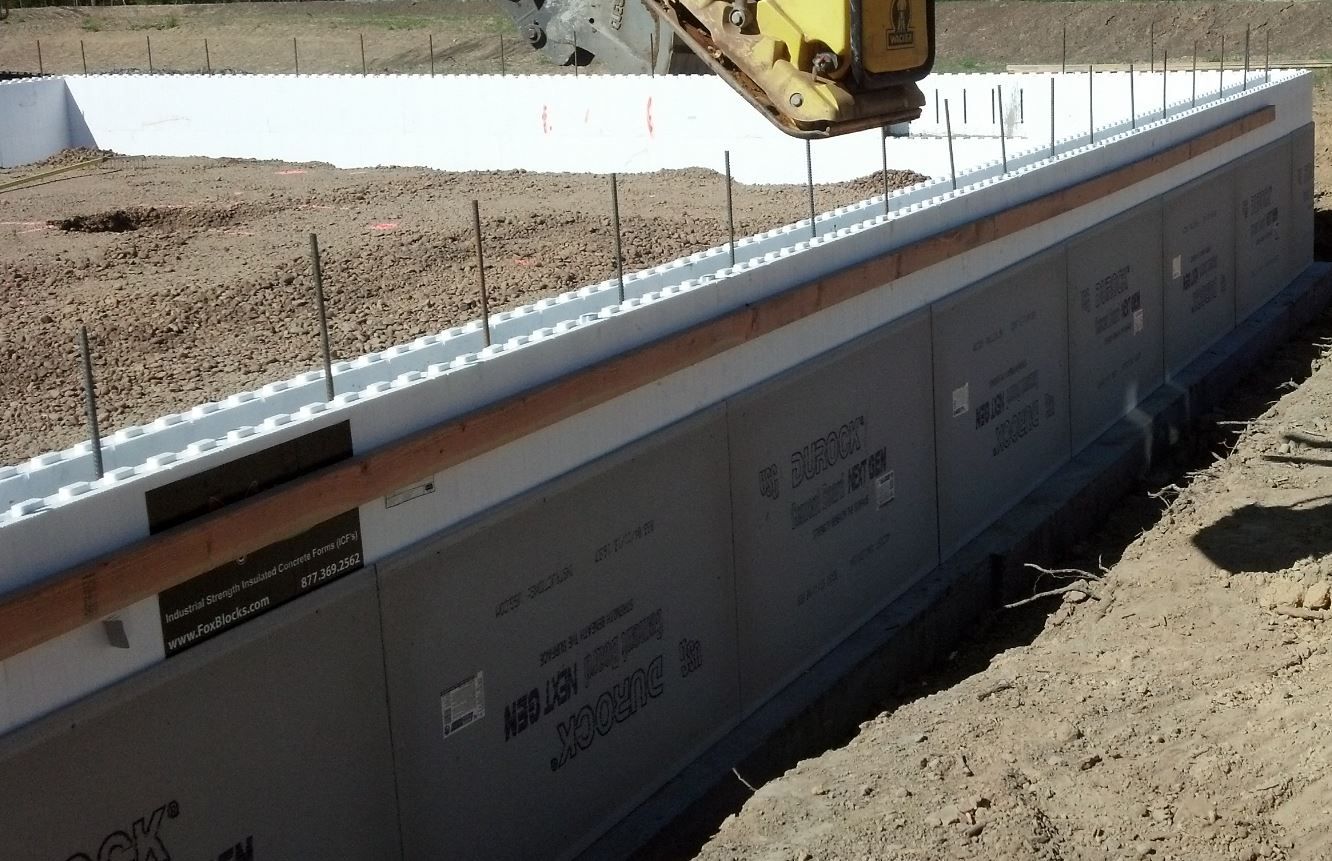
ICFs build durable and energy-efficient below-grade walls. ICFs provide an excellent curing environment for concrete walls, resulting in a foundation with nearly double the compressive strength of a poured concrete foundation. ICF foundations are typically 6 or 8-inch reinforced concrete. ICF foundations also provide disaster-resistance, protecting against fire, wind, and earthquakes.ICF foundations provide superior insulation (R-values greater than R-20), incorporating continuous insulation with few to no thermal bridges.
Construction of an ICF foundation involves dry-stacking blocks to a foundation’s length, then the next step is to reinforce and brace. Workers carefully pour concrete into the hollow form blocks. It’s important to know that pouring concrete into the ICF can occur at ambient temperatures as cold as 5°F. ICFs are a fast and straightforward method of foundation construction. Below-grade ICF construction requires a waterproofing membrane and a reliable drainage system to reduce the possibility of moisture intrusion.
Fox Blocks ICFs: The Best Material Choice for Home Foundations
We can show you how to improve your construction business with ICF foundations, saving you time and money. Compared to other concrete wall foundations, Fox Blocks ICFs is a superior solution to foundation walls.
Fox Blocks Hasten Construction Time
The fast and straightforward installation of Fox Blocks ICFs lessens labor costs and construction risks over other concrete foundation types. The Fox Blocks all-in-one wall assembly combines five construction steps into one, including structure, insulation, air barrier, vapor retarder, and attachment. This feature significantly accelerates project delivery by eliminating the need to coordinate multiple trades while achieving the foundation goals.
Moisture-Resistant Fox Blocks Create Durable Foundations
The Fox Blocks wall system includes a vapor retarder that effectively resists moisture intrusion over CMU and poured concrete wall foundations. Fox Blocks ICF foundations are also less likely to shift in the ground than CMU and poured concrete wall foundations. Shifting walls leads to moisture problems and potentially costly repairs. The forms used in ICF construction protect the concrete, making them less prone to cracking and leaking than poured concrete foundations.
Fox Blocks Below-Grade Walls Create Warm-Dry Spaces
Fox Blocks ICF foundations have an R-value of 23, ensuring warm, comfortable living and storage spaces that save on energy and money compared to other foundations.
Why Choose Fox Blocks Foundations for Your Next Home Foundation
A foundation built with Fox Blocks ICFs simplifies construction, lowering costs, saving time, and lessening long-term problems over other foundation materials. Fox Blocks create warm, dry, healthy, and quiet below-grade spaces.
Contact Fox Blocks experts today so we can show you how commercial construction can improve your business and why Fox Blocks ICF is the best solution for building basement and crawl space foundations.