
Reduce Commercial Building Construction Costs with ICF

Understanding the cost to build a commercial building is essential for contractors aiming to manage expenses efficiently. Fox Blocks Insulated Concrete Forms (ICFs) help commercial contractors lower building costs by reducing labor needs and combating increasing materials costs. Unlike other volatile prices for wood and steel, Fox Blocks has stable and consistent pricing to help ensure accurate project estimates and long-term financial savings for building owners due to their durability, energy efficiency, and disaster resistance.
Growth of the Commercial Building Market
Even with increasing construction costs, the commercial building market shows no signs of slowing down. In fact, one report predicts that by 2050, commercial building floor space will reach 126.1 billion square feet - a 36 percent increase from 2018. The booming commercial construction market provides many opportunities for builders; however, managing the fluctuating material costs, along with labor shortages, can make it difficult to estimate a project to ensure a reasonable profit.
Understanding Commercial Building Construction Costs
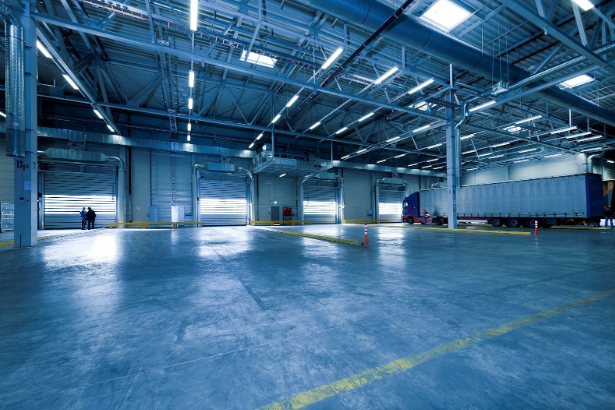
Nationwide, constructing commercial buildings costs an average of $350 per sq. ft. However, the actual cost can vary significantly due to the price of land, permits, local labor, costs, and materials. Here's a breakdown of average costs by region and building type:
Regional Cost Variations:
South: $240 to $680 per sq. ft.
East: $350 to $870 per sq. ft.
Cost by Building Type:
Office Buildings: $240 to $1,000 per sq. ft.
Schools/Universities: $300 to $840 per sq. ft.
Manufacturing Facilities: $210 to $800 per sq. ft.
Hospitals/Clinics: $450 to $1,020 per sq. ft.
Hotels: $130 to $550 per sq. ft.
Apartment Buildings: $150 to $400 per sq. ft.
Community Buildings: $430 to $1,270 per sq. ft.
Shopping Centers: $370 to $580 per sq. ft.
Parking Garages: $70 to $210 per sq. ft.
Rising Building Material Costs in 2024
Construction material prices continue to rise in 2024 due to several factors.
The market has experienced stabilization but still faces challenges like supply chain disruptions, geopolitical tensions, and natural disasters.
Material costs are projected to increase between 2% and 6%, with specific components like electrical products seeing notable price hikes.
Higher labor costs, driven by a shortage of skilled workers, further exacerbate the issue.
Additionally, increased public-funded construction projects maintain high demand for materials, which prevents significant price reductions.
By incorporating ICF solutions like Fox Blocks, commercial contractors can mitigate these rising costs and bring greater financial predictability to their projects.
Increasing Labor Construction Costs
In the U.S., the construction industry faces a significant workforce shortage, with an estimated need for 501,000 additional workers in 2024. This shortage is attributed to high retirement rates among older workers, insufficient younger workers entering the field, and complex immigration policies.
To address this issue, many contractors have increased base pay and offered bonuses and incentives to attract skilled labor, which subsequently raises construction costs. The industry's labor shortage challenges are exacerbated by the ongoing high demand for construction services.
How Fox Blocks ICFs Can Reduce Commercial Building Construction Costs
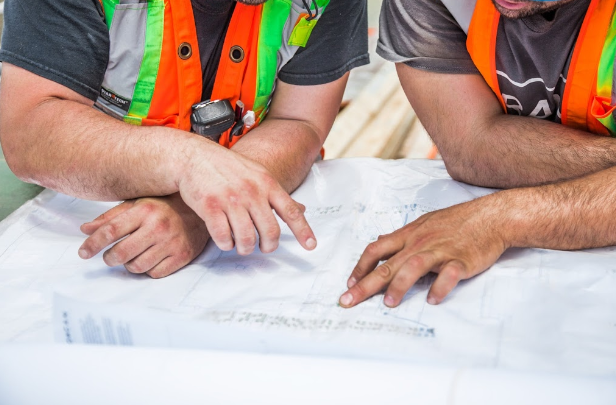
The cost volatility of wood and steel makes estimating a commercial building project challenging. Builders should consider an alternative structural wall product like Fox Blocks Insulated Concrete Forms (ICFs). Made from two sheets of expanded polystyrene (EPS) foam insulation secured with a proprietary tie system and filled with reinforced concrete, ICFs provide stable pricing that ensures more accurate estimates and a secure, profitable bottom line.
Stability in Fox Blocks Pricing
The materials used in Fox Blocks ICFs are less susceptible to market fluctuations compared to traditional materials like steel and lumber. This stability in pricing is due to the consistent availability and cost of polystyrene and concrete, which are less impacted by geopolitical tensions and trade conflicts.
Labor Efficiency with Fox Blocks ICFs
Additionally, using Fox Blocks ICFs can result in significant labor savings. The blocks are designed for easy stacking and interlocking which reduces the need for skilled labor and shortening construction timelines. This efficiency helps mitigate the impact of labor shortages and rising wages in the construction industry, which further contributes to cost savings for commercial building projects.
Fox Blocks Provides Long-Term Benefits to the Commercial Building Owner
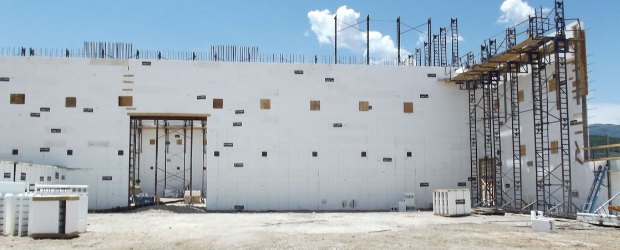
The long-term financial benefits of Fox Blocks ICF commercial buildings make them the superior wall system for commercial construction.
Moisture Resistance
Moisture-resistant commercial buildings require minimal maintenance and repair because they resist mold, mildew, rot, and degradation over the lifespan of the building.
Disaster Resistance
ICFs stand up to natural disasters, which can save building owners money by reducing, if not eliminating, the need to repair and rebuild after storms, fires, or earthquakes.
Energy Efficiency
Fox Blocks create energy-efficient commercial buildings, which save money and benefit the environment. These buildings are designed to reduce heating and cooling costs dramatically, to contribute to long-term energy savings.
Indoor Environmental Quality
ICF buildings produce commercial spaces with excellent indoor environmental quality by improving occupant comfort and productivity while reducing employee sick days. This leads to a healthier and more productive work environment.
High Performance and Market Value
High-performance commercial buildings, like those built with ICFs, have improved occupancy rates, higher rents, and higher market values than conventionally constructed buildings. This makes them an attractive option for both contractors and investors.
Cost and Labor Savings
Commercial building contractors looking to mitigate increasing construction costs due to labor and materials should choose Fox Blocks ICFs for their projects.
Wall systems install easily and requires less labor than traditional building methods, such as wood, steel, and CMU
Reduces labor costs and shortens construction timelines
Stable pricing, which allows for more confident estimates and assured profit
Materials are less susceptible to market fluctuations compared to traditional materials like steel and lumber
Optimize Your Commercial Building with Fox Blocks
Fox Blocks offers a proven track record of expediting construction schedules that result in faster occupancy compared to conventional systems. Our ICF solutions translate into significant cost savings and enhanced building performance for contractors and owners alike.
Contact us today for more information.