
5 Considerations for Your Next Convenience Store Construction Project

A boom in convenience store construction projects, over the last three decades, has nearly doubled the number of stores from 90,900 in 1985 to 153,237 stores in 2019. Builders, designers, and developers of convenience stores can expect this trend to continue due to the ongoing financial success of these stores. 2018 marked 16 straight years of record in-store sales, with total sales in 2018 soaring 8.9 percent to $654.3 billion.
Builders and designers that hope to benefit from the projected need for new convenience stores must recognize how convenience stores have changed over the years. The first convenience stores were just tiny 1200 square foot buildings, selling a handful of snacks, with a single gas pump island. Today’s convenience stores require nearly 5,000 square feet and sell fresh foods, fruit, gourmet coffees, and more; with as many as 10 or more gas pumps.
Besides the increasing size of convenience stores, other crucial considerations for designing and constructing a new convenience store include the rising cost of convenience store construction and the need for energy-efficient and disaster-resistant convenience store construction.
Five Considerations for Your Next Convenience Store Construction Project
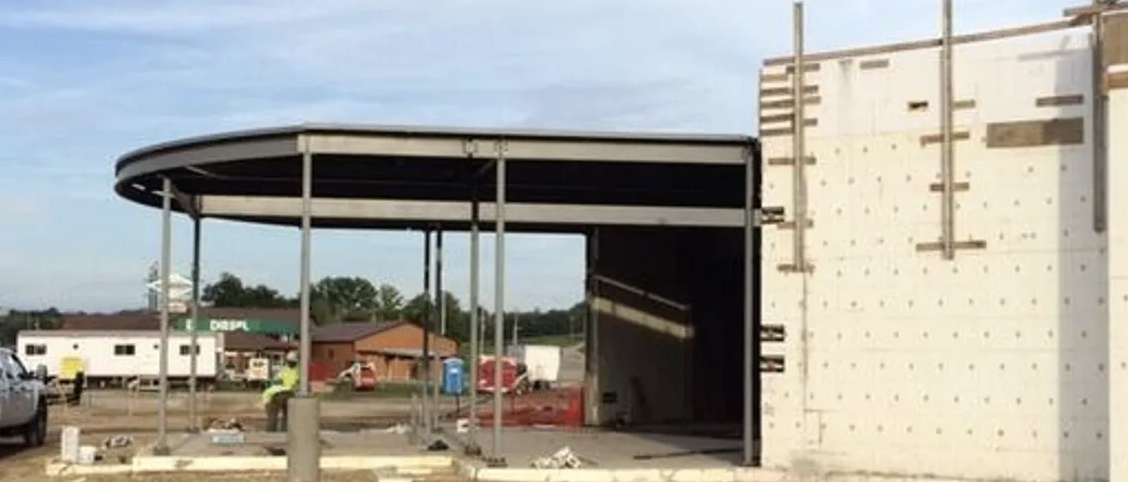
1. The Increasing Costs of Building Convenience Stores
The cost to build a convenience store has surged over the last five years from $5.6 million to $7 million. As reported by the National Association of Convenience Stores (NACS), construction costs for convenience store construction in urban locations skyrocketed by 44.5 percent in the last four years; this compared to 2.7 percent in rural areas. The rising cost of building products (some subject to tariffs) and a shortage of construction labor lead to these soars in construction costs.
2. Designing Energy-Efficient Convenience Stores
Increasingly, convenience retailers focus on managing long-term energy costs through energy-efficient construction; a trend mainly due to the amount of energy required to operate these stores. While the average food store uses about 51.5 kilowatt-hours per square foot, convenience stores use 94 kilowatt-hours per square foot due to their wall-to-wall refrigerators, outdoor canopy lighting, and 24-hour operation. For long-term operational savings, new convenience store design should include energy-efficient products like LED lighting, energy-efficient refrigeration, and Fox Blocks insulated concrete forms (ICFs).
3. Designing Disaster-Resistant Convenience Stores
During and after a natural disaster, like hurricanes, tornadoes, fire, and earthquakes, convenience stores often become a sanctuary in their communities, providing much-needed fuel and food to residents and first responders. So it is imperative that the design of new convenience stores must protect the structure and its occupants against disasters. in 2018, NACS developed resources to help convenience retailers plan, prepare, and recover from a natural or man-made disaster.
4. The Increasing Size of Today’s Convenience Stores
The addition of extended food services in convenience stores demands bigger stores than those in the past. The average convenience store is 3,230 square feet. However, new convenience store projects require more square feet, with touch screen food-ordering kiosks, open kitchen designs, and seating areas. In rural locations, convenience stores average 4,991 square feet, while in urban neighborhoods, the stores average 4,603 square feet.
5. Why Choose Fox Blocks ICF for Your Next Convenience Store Construction Project
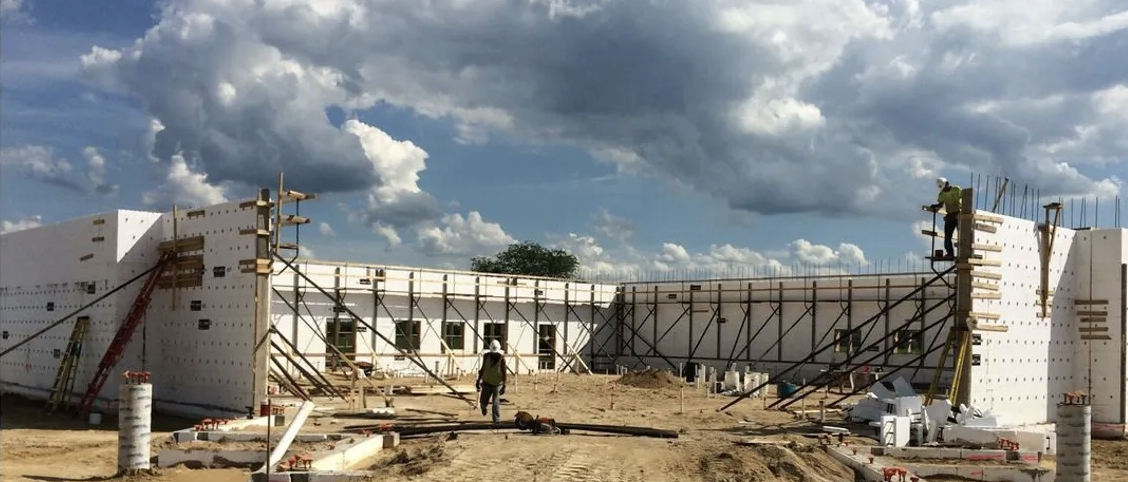
Fox Blocks ICF construction provides an excellent choice for new convenience store construction. Fox Blocks construction reduces labor costs, provides design versatility, and creates energy-efficient and disaster-resistant convenience stores.
- Fox Blocks reduces building costs because Fox Blocks includes an all-in-one wall system that integrates five steps into one quick, easy, and safe installation.
- The versatility of Fox Blocks ICF construction allows many possibilities for size, wall heights and style of convenience store design.
- Fox Blocks ICF enhances the building envelope, creating an energy-efficient convenience store with an R-Value of 23. They also provide continuous insulation, no thermal bridging, beyond code minimum air tightness and eliminate mold and mildew from moisture within the wall assembly.
- Fox Blocks build disaster-resistant convenience stores. Fox Blocks are wind-resistant, fire-resistant, and earthquake-resistant.
- Fox Blocks provides a solid substrate for the direct application any exterior or interior finish.
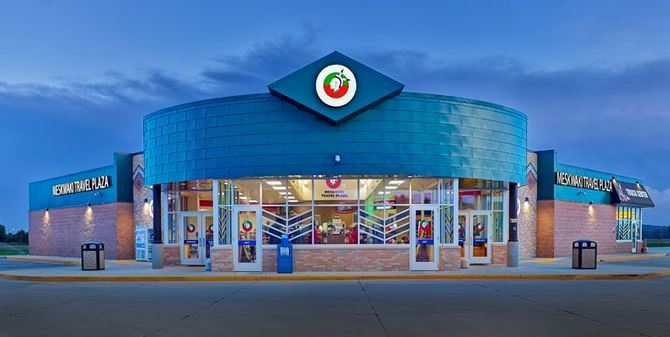
The Meskwaki Travel Plaza provides a full-service travel center that includes a truckers’ lounge, showers, laundry facility, convenience store, a 50’s themed diner, and even a smoke shop.
The original design for the Plaza called for CMU (Concrete Masonry Unit); however, the final plan choose Fox Blocks ICF construction. As a result of using ICF construction, the project was completed in less time and under budget enabling faster occupancy. The ICF construction also improved energy savings and reduced sound penetration from passing vehicles. Furthermore, the ICF allowed for a less expensive, thin brick façade than once required for CMU. Fox Blocks, in fact, has proven to provide more than five considerations for any construction project, any size.