
Benefits of Accelerating the Design Process and Construction Completion Schedule

Accelerating construction schedules provides contractors and developers numerous benefits. Quicker construction can save money, avoid problematic weather, and help realize contract bonuses. However, due to a shortage of labor and materials, the current building climate can often delay a project's delivery time. In order to keep a project on time, and possibly accelerate completion, contractors must carefully plan and design their projects, with particular attention to selecting time-saving products like Fox Blocks insulated concrete forms (ICFs).
Accelerating the Construction Schedule
Each phase of a construction project can accelerate the construction schedule, vital to staying on budget and keeping your client happy. The six construction phases are: design/concept formation, feasibility study, schematic design, design development, construction documents, and construction.
A well-thought-out design concept quickens delivery time.
A detailed feasibility study can prevent construction delays.
The schematic design phase allows architects to identify time-saving features.
Fox Blocks ICFs can accelerate the design development phase.
Fox Blocks ICFs will expedite the construction document phase.
Quick and easy to install ICFs reduce the time for the construction phase.
Design Concept
Developing the design concept requires the entire building team to brainstorm, discuss, and collaborate to precisely define the construction project's ideas, goals, and needs. The concept should include a simple set of guidelines from the schematic design phase through construction completion. Sticking to the guidelines and the project’s defined goals and needs will hasten decision-making and accelerate construction completion.
Feasibility Study
A feasibility analysis accesses a project’s potential technical, financial, operational, scheduling, and legal success. A detailed feasibility study reveals the project’s parts most at risk for scheduling delays, allowing the building team to address potential issues before the project begins﹘vital to maintaining, if not hastening the construction timeline.
Schematic Design
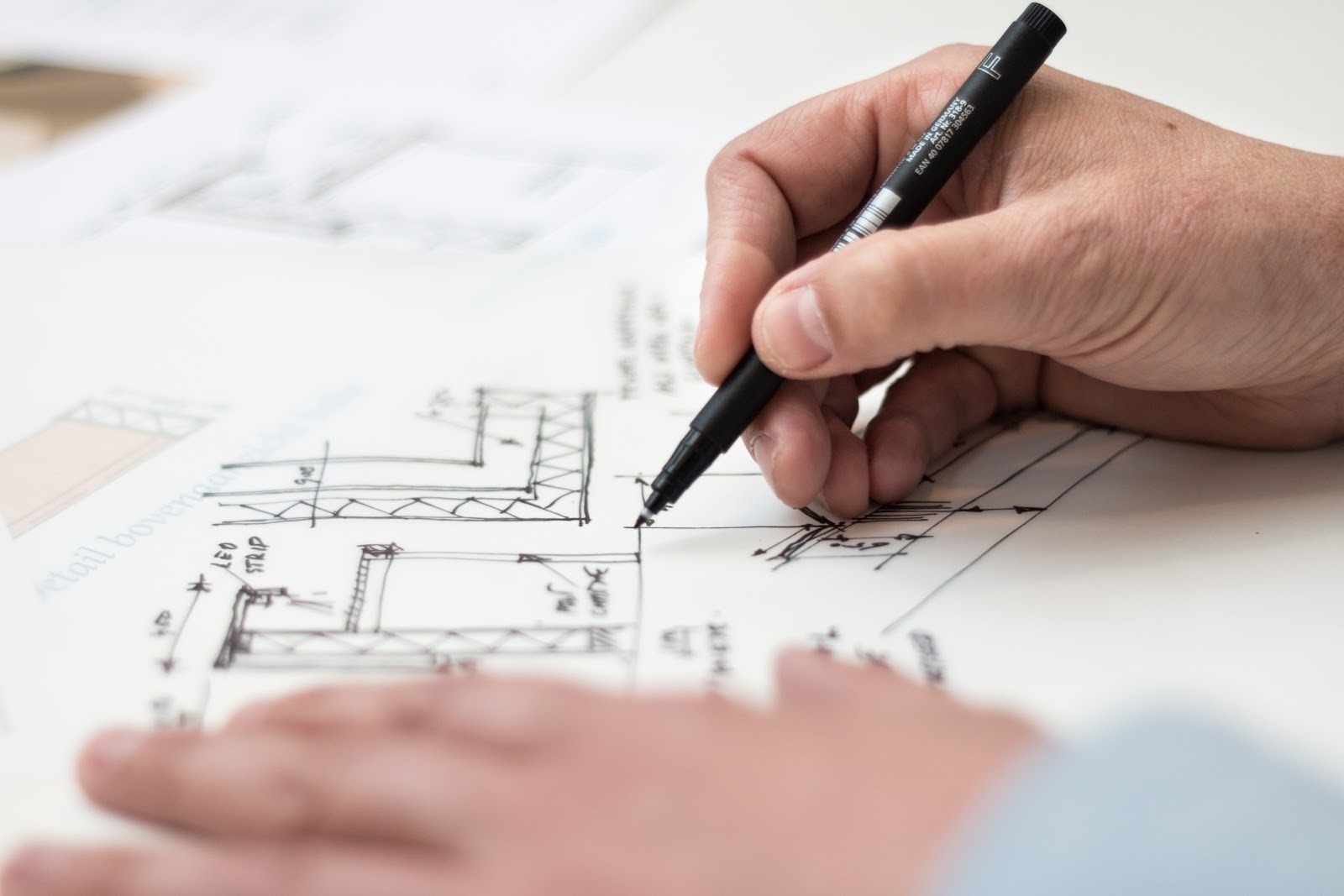
During the schematic design phase, the building team and client present the project’s design concept to the architect. The team will also specify the end-product requirements like eco-friendly concerns, energy-efficient design, and cost limits. The architect uses the information to produce rough computer renderings or illustrative sketches of the floor plans, elevations, and site plans. The project moves forward once the building team, client, and architect agree on the drawings that best represent the project's desired goals.
A complete and accurate schematic design will confirm the building’s square footage and estimate the project's budget. It also establishes the project’s timeline and completion date, identifying parts of the project that can expedite completion and limit unexpected and costly delays.
Design Development
The architect or design team more fully defines and develops the project's significant aspects during the design development phase, including the exterior, interior layouts, room sizes, and material for the roof assemblies, floors, structure, and walls. They will also assess the interface between materials and assemblies and the functionality and resilience of the building. In addition, the engineers will further develop the HVAC, plumbing, and electrical systems.
The design development phase delivers a more detailed set of drawings (than the schematic phase), an updated cost estimate, and a specification book. The specification book contains selected materials relevant to the design, installation introductions, quality control requirements, and other technical information.
A building team’s knowledge and expertise of the most current products and application procedures is vital during the design development phase - due to the complexity of today’s building envelope and the need to meet new building and energy codes for airtightness.
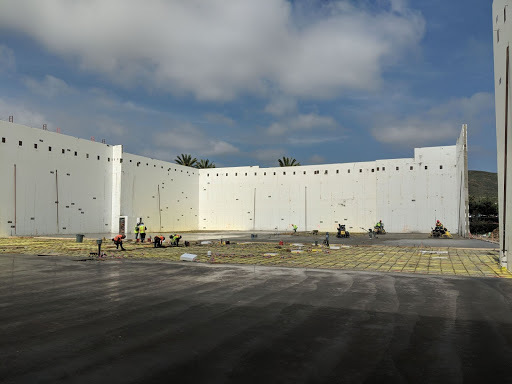
The wall assembly dramatically impacts the performance of the building envelope. The wall assembly product should provide six essential characteristics to ensure a tight building envelope:
1. Thermal efficiency
2. Airtightness
3. Moisture and vapor protection
4. Weather barrier
5. Structural capability
6. Resiliency – high winds and seismic
Evaluating a wall assembly's capabilities to meet these characteristics requires a whole-building approach ﹘ in other words, knowing how all the building products interface with the wall system and connect to ensure an air-tight building envelope. Unfortunately, the time-consuming process of finding a wall system that meets all six requirements can prolong the design development phase.
How Fox Blocks Quickens the Design Development Phase
Fox Blocks ICFs all-in-one wall system achieves all six requirements, accelerating the design development phase by utilizing one material. Traditional wall systems require a building team to decide on five or six different materials. Fox Blocks wall assemblies meet or exceed the high-performance wall assembly requirements for residential and commercial designs of all sizes and shapes, solving many design attributes for today’s building envelope.
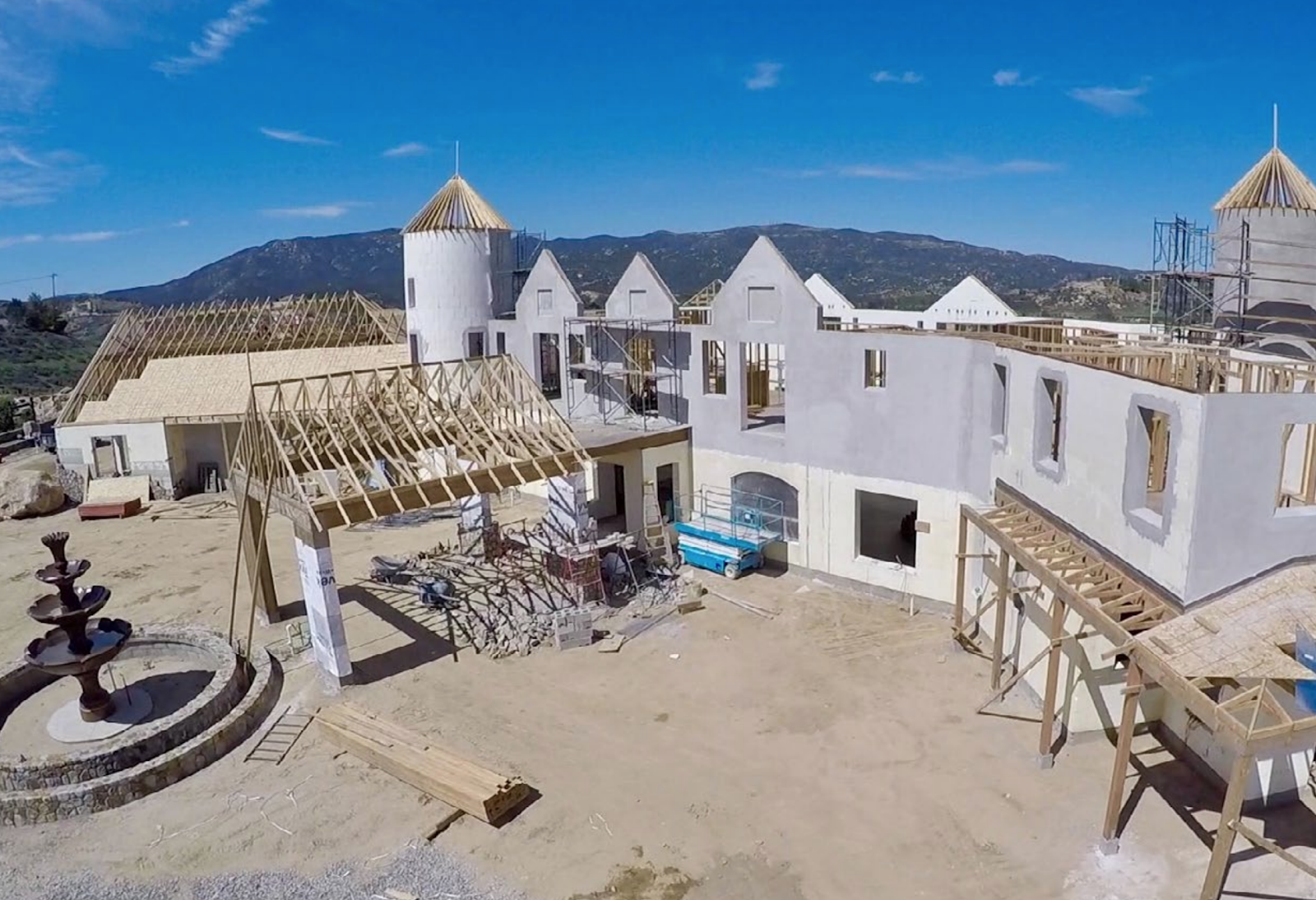
Construction Document
The construction document phase finalizes all of the necessary technical information into a final-complete set of drawings and specifications, including the requirement to obtain a building permit from the local-jurisdiction authority. Typically, the architect addresses the authorities' questions, requests additional information or changes/corrections to the drawings. The contractor then uses the drawings to submit bids/quotes, in order to produce an updated cost estimate.
Once the final drawings are complete, including the layout, structure, and materials, the architect can detail how the contractor will put together the building.
How Fox Blocks ICFs Expedites the Construction Drawing Phase
A traditional wall assembly requires multiple materials (and trades) to satisfy all the structure and building science elements. The architect needs to include these materials in the plans, detailing the interfacing of how to install, connect and seal ﹘a precise and time-consuming process.
Fox Blocks single product wall assembly accelerates the construction documents phase, moving up the bidding timeline and construction start date. Fox Blocks further hastens the construction drawing phase by offering a vast CAD and BIM library that simplifies the drawing process for plans, wall sections, and details. A library of ICF standard details, plus BIM files, makes it easy to formulate project construction drawings.
Construction Phase
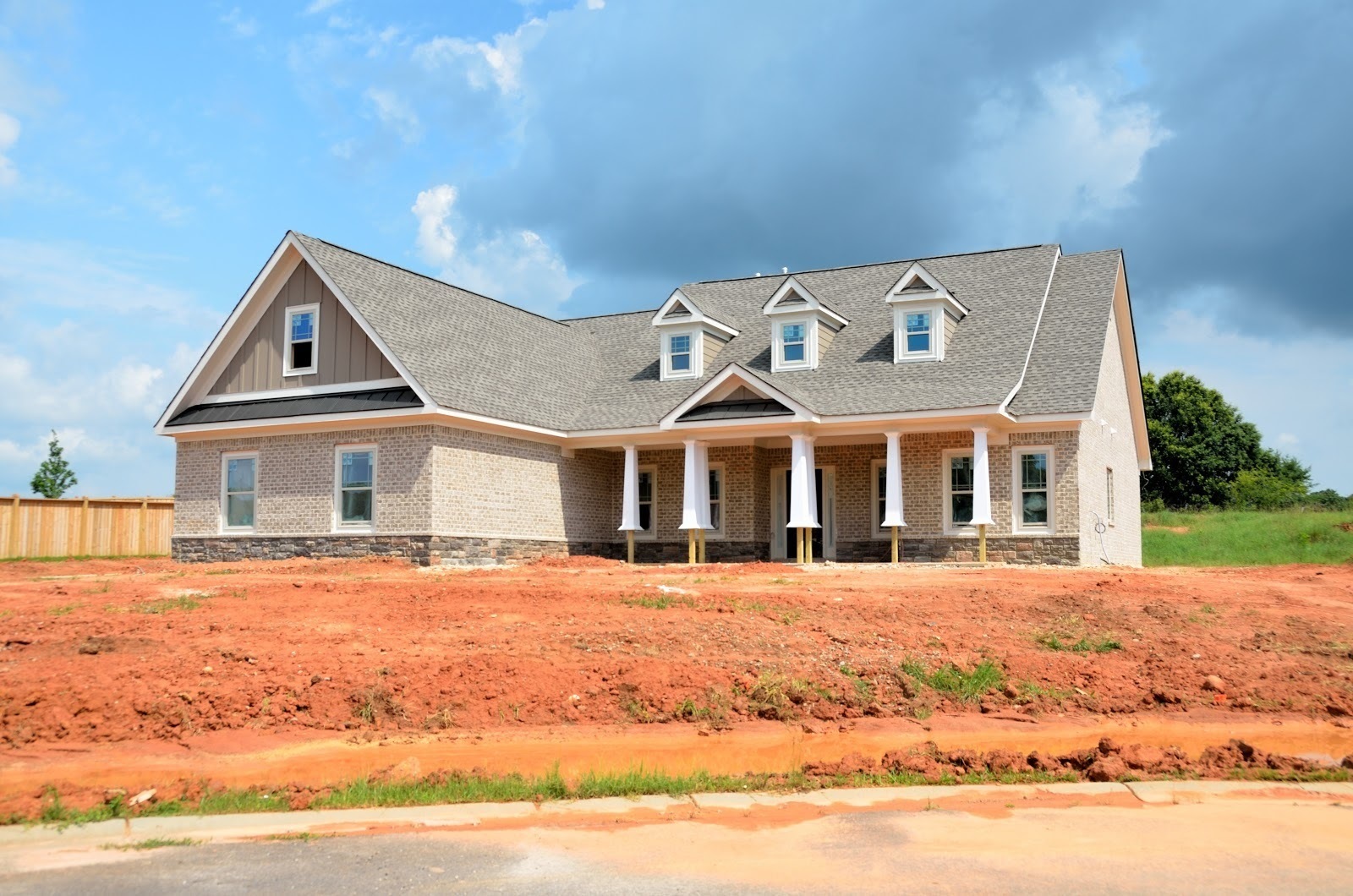
The construction phase completes the building and the scope of the project. Most of the construction phase occurs linearly, meaning you must complete one portion of the construction process before starting another. Each phase usually requires different subcontractors. The more subcontractors involved in a project, the more coordination is required, further impacting the schedule, which often delays delays. According to the timeline, a builder's success depends on moving the project from start to completion or occupancy, so delays for any reason are problematic.
Quick and Easy to Install Fox Blocks ICFs Reduce Construction Time
Fox Blocks ICFs are a faster way to install below- and above-grade walls than traditional methods like poured concrete and stick-built frames.
Fox Blocks below- and above-grade walls combine five-building steps into one: air barrier, structure, insulation, vapor retarder, and attachment. The all-in-one wall system reduces the need to coordinate multiple trades, significantly accelerating delivery time while achieving the wall system’s goals. The Fox Blocks ICF wall system also creates a weathertight structure in a shorter time than a conventional wall.
Time is the most important component in the construction phase. Advancing the completion date and occupancy by weeks or months has proven results by implementing Fox Blocks in the design and construction process for all building types.
Accelerate the Design Process and Construction Completion with Fox Blocks ICFs
Fox Block ICFs can accelerate construction schedules during most building phases, helping a contractor stay on budget and hasten delivery time. Specifically, Fox Block ICFs all-in-one wall systems accelerate the design development and construction drawing phases by eliminating the building team's need to decide, design, and bid on the five or six materials required for a traditional wall system. Moreover, Fox Block ICFs Fox Blocks quick and easy to install all-in-one wall system reduces the need to coordinate multiple trades, significantly accelerating the construction phase.
The Fox Blocks website has a full resource library on the product line, code evaluations, testing, and building science attributes of ICF. Fox Blocks ICF meets the multiple requirements for above- and below-grade wall assemblies for all building types and climate zones. The simplicity of construction drawings available in our CAD and BIM libraries will help expedite the design process.
Fox Blocks ICFs provide many time-saving advantages that are sure to accelerate your next energy-efficient building project's design process and construction completion.
Contact the ICF experts at Fox Blocks today to take the first steps toward a faster construction process.