
5 Ways To Save Money On Your Next Commercial Project

As builders and buyers are forced to continually fight rising labor and materials costs in the construction industry, making small changes, minor substitutions and looking for ways on how to save money on commercial projects are more important than ever. Putting thought into the final costs of a build during the early design phase can save you headaches and hassles regarding your budget.
Focusing on things like planning the budget accordingly, leaving additional funds for unforeseen circumstances, having a trusted team who communicates well and using efficient materials, such as Insulated Concrete Forms (ICF), are important suggestions to consider.
ICF’s benefits are massive, ranging from cost savings to durability, high quality and easy installation. If you want to learn how to save money on your next project, keep reading.
The Struggles of Staying on Budget on Commercial Projects
Staying on a strict timeline and tight budget is incredibly hard on commercial projects. Commercial projects require a large team across various specialties and trades, and in comparison to residential projects, there is a bigger chance for delays that increase the budget.
“About 75% of the time,” said Steve Summers to Construction Dive, Executive Vice President of Gray Construction in Lexington, Kentucky, “there is some level of unanticipated or unforeseen conditions encountered on a construction job site.”
While there are definitely struggles you have no control over that impact your budget, there are other ways you can save both money and time on your next commercial project.
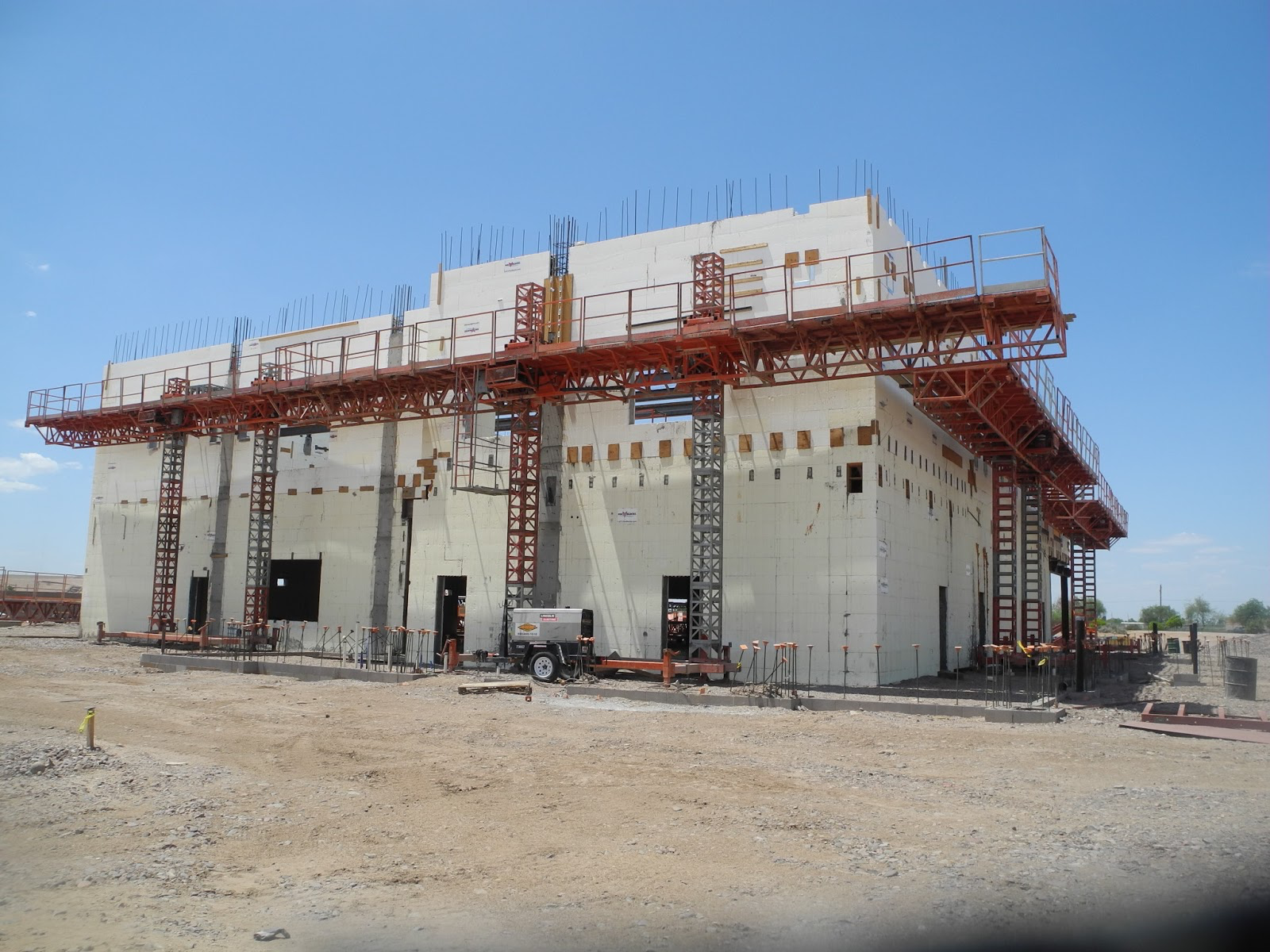
5 Ways to Save Money on Your Next Commercial Project
1. Define Your Workflow and Your Budget
The first thing you can do is plan your budget accordingly, making sure you leave room for additional funds for any unforeseen circumstances.
You should make sure you have a defined workflow to help you optimize your time, reduce ineffectiveness, pinpoint bottlenecks and redundant tasks to remove them and give you a fine-tuned project. Saved time equals saved money.
2. Have a Trusted Team of Professionals
Make sure you have a trusted team working on your project, one that is able to communicate any issues properly and promptly. In the construction industry, the trend towards more specialized material and applications challenges contractors to hire an increasing number of subcontractors.
For instance, the complexity of concrete and masonry foundations requires the specific skills of experienced workers, along with specialized equipment. The more specialized material you have, the larger your team, the harder it is to keep efficient and effective communication.
Using materials that don’t require specialized trades to install can help reduce the size of your team, keeping it to those you trust to do the best job possible.
3. Find Materials and Supplies That Require Less Specialized Trades
Labor shortages, especially for skilled workers, are still very widespread right now. Because of these shortages, builders are having to pay higher wages and accept high subcontractor bids, leading to higher labor costs and overall budget.
The National Association of Home Builders reports that today's builders often employ 20 or more subcontractors, resulting in 75 percent of the total construction cost. What if you could decrease your number of trades necessary, thereby decreasing the number of subcontractors?
4. Use Efficient Materials Like ICF
During the design phase, look into more efficient materials, such as ICF. ICFs are hollow blocks made with expanded polystyrene insulation or other insulating foam. They are stacked to form the shape of building walls with steel rebar for reinforcement. Pouring concrete into the hollow centers creates interior and exterior layers of continuous insulation and lessens any thermal bridging through the wall.
Fox Blocks’ ICF walls install quickly and easily — saving you time and money by reducing labor costs, eliminating the need for several different subcontractors and hastening project delivery time. In fact, a Fox Blocks wall can cost 20% less to build than either a concrete block or poured concrete foundation wall.
How can that be? The Fox Block wall assembly combines five building steps into one: the structure, insulation, air barrier, vapor retarder and attachment. This significantly quickens project delivery time by eliminating the need to coordinate multiple trades.
ICF construction provides flexibility in design, whether your design calls for tall walls, large openings, below-grade or multiple stories. Fox Blocks ICF construction’s simplicity and speed will set any contractor’s mind at ease when it comes to creating straight and plumb ICF foundations.
Have ROI at Top Of Mind
Not only are ICF construction costs lower, but it also provides you with a durable and high-quality building material. ICF blocks are long-lasting products that lessen replacement and maintenance costs and are disaster-, moisture-, pest-, fire- and UV-resistant: ICF construction ROI is unparalleled.
To show you how Fox Blocks can help you save money on your next commercial project, check out how Fox Blocks helped Holiday Inn save money on their project.
The Centre Park Holiday Inn Event & Conference Center is a 116,000 square foot event center. Using Fox Blocks contributed to saving over two months in construction scheduling, fully completing the project in just 420 days, saving them thousands of dollars. You can learn more about the case study here.
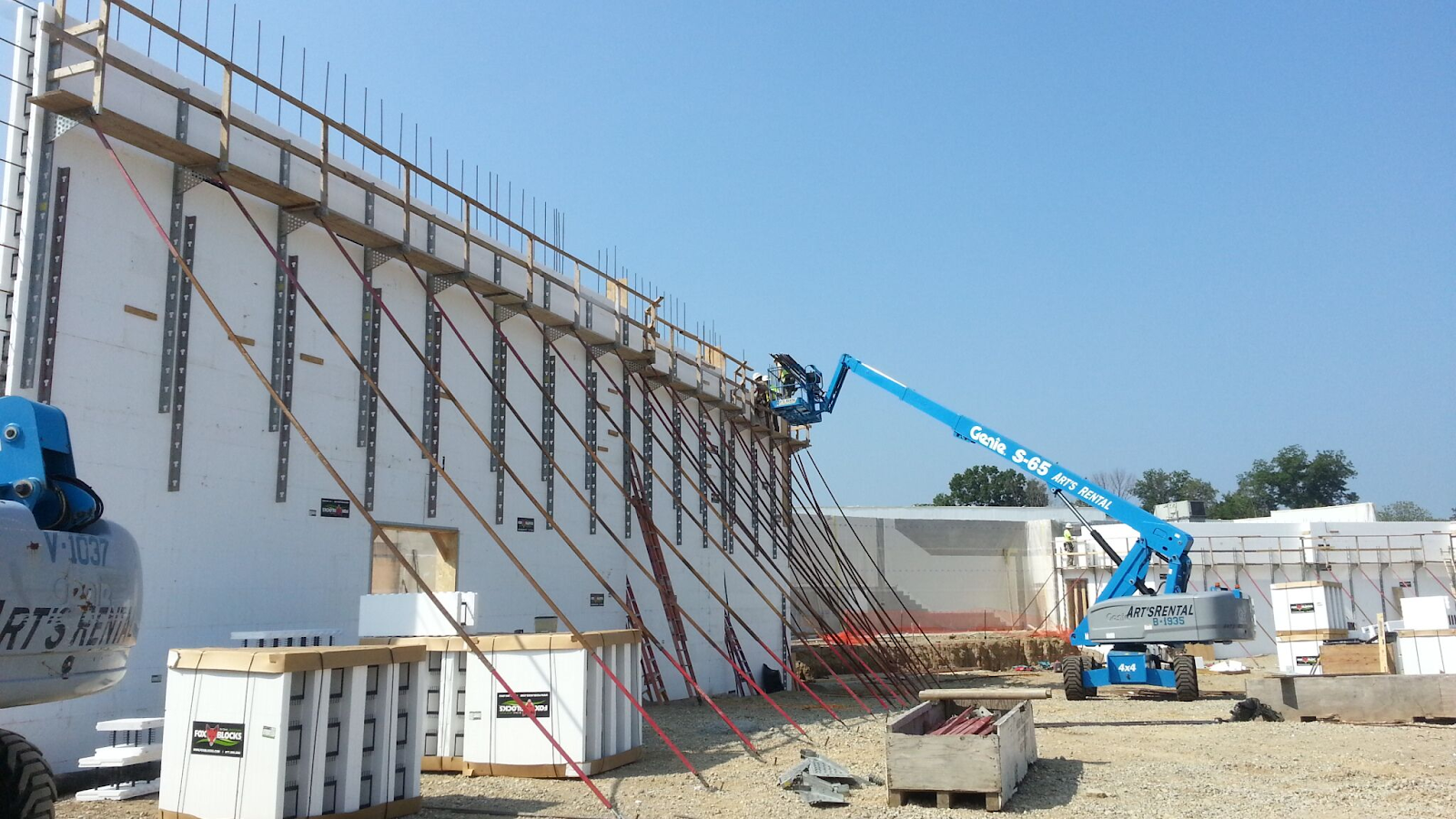
Want to learn more about ICF and how it can save you money on your next commercial project? Check out Fox Blocks’ product offerings or contact us today to talk to an ICF expert.